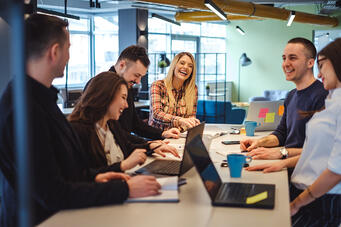
The Northeast's regional leader in waste management is the Casella trash company. The company was recently accused in three states of violating labor law. The stock rose 540% to $54 million after the company announced that it was consolidating its operations. The CEO claims that hard work pays off.
Casella violated all three state labor laws
Three former drivers of Casella Waste Systems in Rutland are suing the company for allegedly violating labor laws. They claim that the company did not pay them for overtime and deducted their 30-minute meals breaks from their wages. Casella required drivers that they inspect the vehicles before and afterwards each trip. The plaintiffs are seeking damages and attorneys' fees.
Casella is an important regional player in Northeast's waste system
Casella, one of the leading regional players in waste management, has operations in New England, New York, and Pennsylvania. The company has a number of landfills, transfer station and recycling facilities. Its Rutland site is Vermont's largest open landfill. It is publicly traded, and it expects to generate $774 million in 2020. The company will report its latest earnings after the markets close.
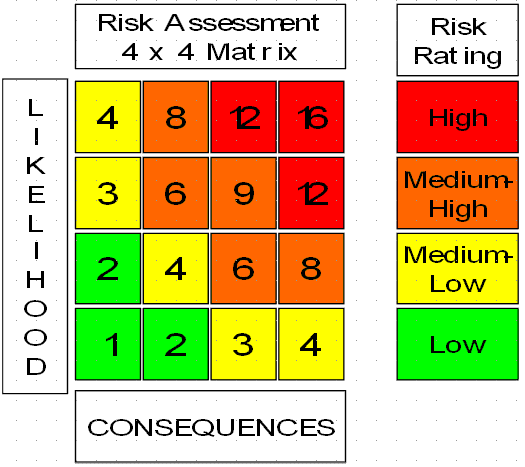
Casella stock has risen 540% since it consolidated its operations
With a market capitalization in excess of $1.8billion, the company's stock now trades at new highs. After a series of mistakes over the years, the company has made a comeback and is now one the largest garbage haulers in New England. The company's founders, Doug and John Casella, are among the wealthiest people in the state, and they are also involved in the day-to-day operations of the company.
Casella's CEO affirms that hard work pays off
Casella is an organization that manages waste and recycles resources. World Finance Magazine recently ranked Casella as the most sustainable company within its industry. The company has achieved numerous record-setting accomplishments thanks to its commitment to sustainability and hard work.
Casella's stock closed at 55 cents per share
This was the lowest stock price in company history. It closed at 55c per share on March 12, 2009. This was an improvement from the more than twentyfold increase in 1997. Casella has a long history of incurring significant debt and has not been financially successful in recent years. However, the company made some changes in its business model to improve its prospects.
Casella's loan to finance a project for landfill development
Casella is using debt to finance its landfill development initiative. It aims to bring that new capacity online by late 2023 or early 2024. Company executives predict further profitability over the next few year and are confident that their business plan can support future expansion.
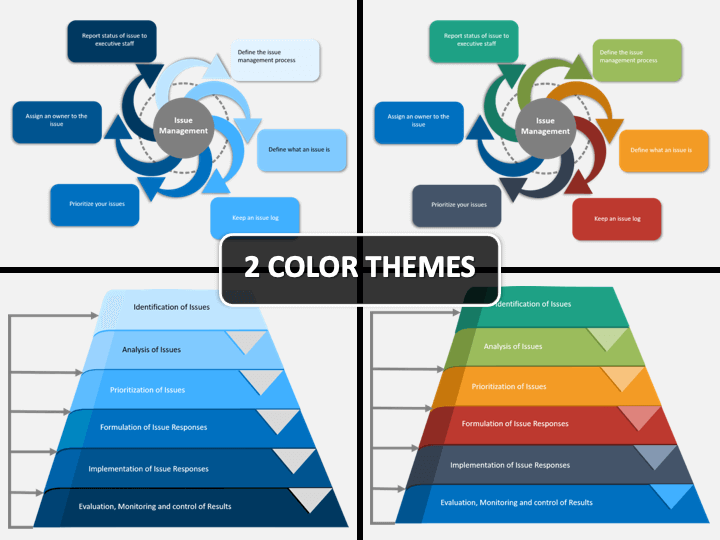
Casella's acquisition spree
Casella's acquisition spree is nothing short of a colossal undertaking. So far, the company has made at minimum six acquisitions and invested into one company. It has spent more than $355million. Casella has invested in a number of different sectors, including waste management, construction and demolition, and plastic raw materials.
FAQ
How does Six Sigma work?
Six Sigma uses statistical analysis for problems to be found, measured, analyzed root causes, corrected, and learned from.
First, identify the problem.
The data is then analyzed and collected to identify trends.
Then corrective actions are taken to solve the problem.
Finally, data will be reanalyzed to determine if there is an issue.
This continues until the problem has been solved.
What is Kaizen and how can it help you?
Kaizen is a Japanese term which means "continuous improvement." This philosophy encourages employees to continually look for ways to improve the work environment.
Kaizen is based upon the belief that each person should be capable of doing his or her job well.
What are the three main management styles you can use?
There are three types of management: participative, laissez faire, and authoritarian. Each style is unique and has its strengths as well as weaknesses. Which style do your prefer? Why?
Authoritarian – The leader sets a direction and expects everyone follows it. This style works best in large organizations that are stable and well-organized.
Laissez faire - Each individual can decide for himself/herself. This style is most effective when the organization's size and dynamics are small.
Participative – Leaders are open to suggestions and ideas from everyone. This style works best in smaller organizations where everyone feels valued.
What are the key management skills?
Management skills are essential for any business owner, whether they're running a small local store or an international corporation. They are the ability to manage people and finances, space, money, and other factors.
When you need to manage people, set goals, lead teams, motivate them, solve problems, develop policies and procedures and manage change, management skills are essential.
As you can see there is no end to the number of managerial tasks.
Why is Six Sigma so popular?
Six Sigma is easy to use and can lead to significant improvements. It also provides a framework for measuring improvements and helps companies focus on what matters most.
Statistics
- As of 2020, personal bankers or tellers make an average of $32,620 per year, according to the BLS. (wgu.edu)
- This field is expected to grow about 7% by 2028, a bit faster than the national average for job growth. (wgu.edu)
- The BLS says that financial services jobs like banking are expected to grow 4% by 2030, about as fast as the national average. (wgu.edu)
- The average salary for financial advisors in 2021 is around $60,000 per year, with the top 10% of the profession making more than $111,000 per year. (wgu.edu)
- Your choice in Step 5 may very likely be the same or similar to the alternative you placed at the top of your list at the end of Step 4. (umassd.edu)
External Links
How To
How do I do the Kaizen Method?
Kaizen means continuous improvement. The term was coined in the 1950s at Toyota Motor Corporation and refers to the Japanese philosophy emphasizing constant improvement through small incremental changes. It's a process where people work together to improve their processes continuously.
Kaizen, a Lean Manufacturing method, is one of its most powerful. The concept involves employees responsible for manufacturing identifying problems and trying to fix them before they become serious issues. This will increase the quality and decrease the cost of the products.
Kaizen is the idea that every worker should be aware of what is going on around them. So that there is no problem, you should immediately correct it if something goes wrong. If someone spots a problem while at work, they should immediately report it to their manager.
Kaizen is based on a few principles. The end product is always our starting point and we work toward the beginning. For example, if we want to improve our factory, we first fix the machines that produce the final product. Next, we fix the machines which produce components. We then fix the workers that work with those machines.
This is known as "kaizen", because it emphasizes improving each step. Once we have finished fixing the factory, we return to the beginning and work until perfection.
How to measure kaizen's effectiveness in your business is essential to implement it. There are many ways to tell if kaizen is effective. One of these ways is to check the number of defects found on the finished products. Another way is determining how much productivity increased after implementing kaizen.
If you want to find out if your kaizen is actually working, ask yourself why. You were trying to save money or obey the law? Did you really believe it would lead to success?
Suppose you answered yes to any of these questions, congratulations! You're ready to start kaizen.