
Retaining employees can be one of the most difficult challenges in human resource management. High attrition rates can be attributed to a number of reasons. Low employee morale, poor management practices and unresponsive managers are just a few of the reasons. HR leaders can increase employee retention and employee motivation by doing a few things.
Attracting top talent
Retaining the best employees is one the biggest challenges for human resource management. Many top talent candidates are seeking meaningful work and positive organizations. They want to be part of something greater than themselves. The most important factor in determining a worker's choice of job is often compensation.
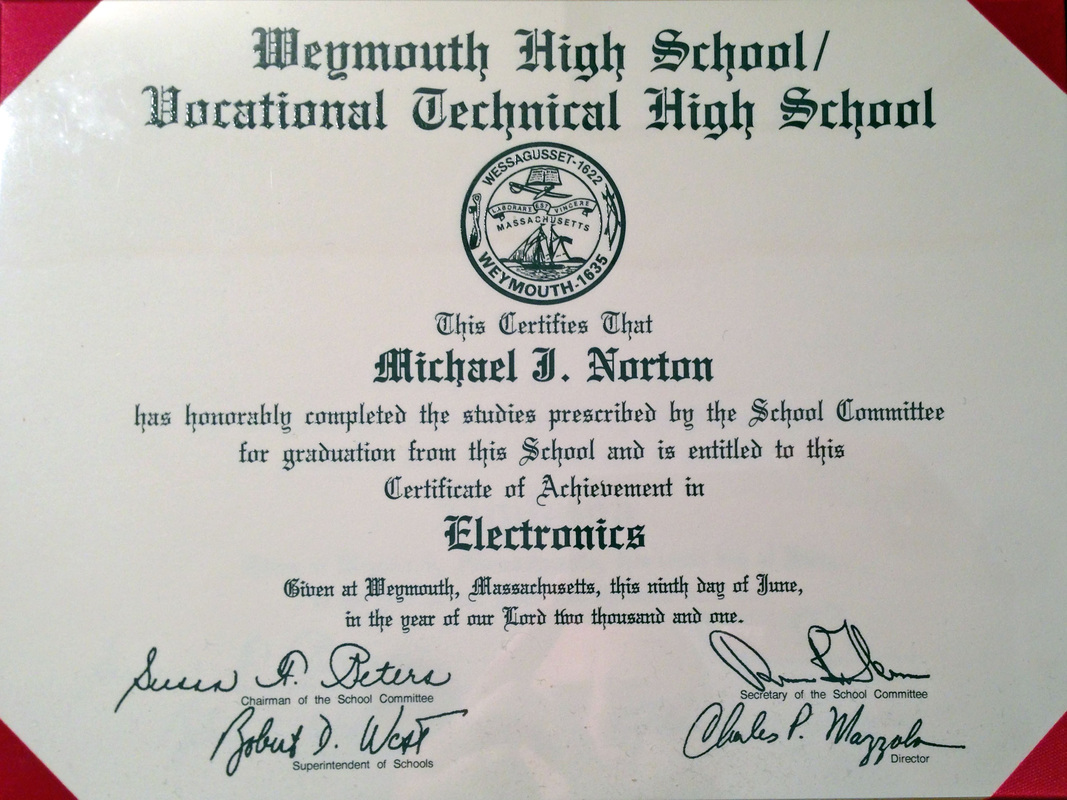
There are a number of different ways to attract top talent to an organization. One option is to host an event at which candidates can get to know the company and meet their employees. This event is especially useful for candidates who live far from the company. Another option is hosting virtual events that allow candidates to get to know your company and the people behind it. These events can also be promoted openly via social media. You may invite other people interested in the company.
Managing costs
Management of human resource management costs requires consideration of many factors. If these factors aren't understood, costs can spiral out of control. It is vital to manage human resource costs. It is the job of HR to manage the company's overall cost. This can be done through a number of different strategies.
Although cutting headcount may seem simple and quick, this approach can cause employees to lose motivation and lead to decreased productivity and reduced competitiveness. Moreover, layoffs can hurt the organization's reputation with customers. Before implementing HR cost-saving ideas, companies should think carefully.
Turnover Management
The high rate of employee turnover is one of the major challenges for human resource management. A high rate of employee turnover is a concern for all businesses as it can negatively impact the bottom line. It is possible to reduce turnover. HR managers can take several steps to reach their goals. The first step is to collect data about turnover rates and determine ways to reduce them. By identifying and tracking turnover rates by department, role, age, and ethnicity, organizations can determine what factors are responsible for high employee turnover. These data can be used by human resource managers and departmental leaders to spot key issues.
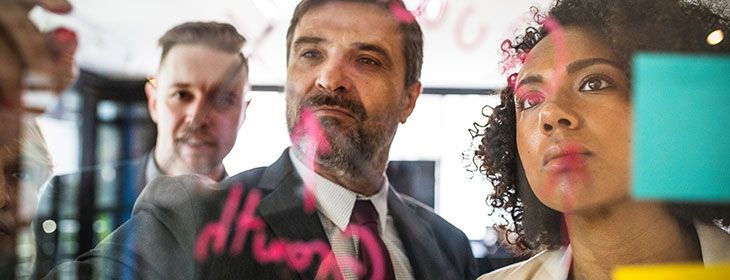
One way to calculate the rate of employee turnover is to measure it in terms of the number of employees who quit in a given period of time. To calculate this, a company should divide its number of employees at start of period by its number of employees at end of period. The Bureau of Labor Statistics publishes monthly reports that describe job openings and labor turnover. Both permanent employees and temporary workers are included in the data. Temporary leave and shifts that are not permanent should not be added to the turnover rate, as this can lead to inaccurate results.
FAQ
Six Sigma is so popular.
Six Sigma can be implemented quickly and produce impressive results. Six Sigma provides a framework to measure improvements and allows companies to focus on the most important things.
What can a manager do to improve his/her management skillset?
Good management skills are essential for success.
Managers must constantly monitor the performance of their subordinates.
You must quickly take action if your subordinate fails to perform.
You should be able to identify what needs improvement and how to improve things.
What is the difference in a project and program?
A program is permanent, whereas a project is temporary.
Projects usually have a goal and a deadline.
It is often carried out by a team of people who report back to someone else.
A program typically has a set goal and objective.
It is usually implemented by a single person.
Statistics
- Hire the top business lawyers and save up to 60% on legal fees (upcounsel.com)
- As of 2020, personal bankers or tellers make an average of $32,620 per year, according to the BLS. (wgu.edu)
- 100% of the courses are offered online, and no campus visits are required — a big time-saver for you. (online.uc.edu)
- This field is expected to grow about 7% by 2028, a bit faster than the national average for job growth. (wgu.edu)
- Our program is 100% engineered for your success. (online.uc.edu)
External Links
How To
How can you use the Kaizen method?
Kaizen means continuous improvement. Kaizen is a Japanese concept that encourages constant improvement by small incremental changes. This is a collaborative process in which people work together to improve their processes continually.
Kaizen is one method that Lean Manufacturing uses to its greatest advantage. Kaizen is a concept where employees in charge of the production line are required to spot problems during the manufacturing process before they become major issues. This improves the quality of products, while reducing the cost.
Kaizen is a way to raise awareness about what's happening around you. If something is wrong, it should be corrected immediately so that no problem occurs. If someone spots a problem while at work, they should immediately report it to their manager.
Kaizen has a set of basic principles that we all follow. When working with kaizen, we always start with the end result and move towards the beginning. If we want to improve our factory for example, we start by fixing the machines that make the final product. Next, we repair the machines that make components. Then, the machines that make raw materials. Finally, we repair the workers who are directly involved with these machines.
This is known as "kaizen", because it emphasizes improving each step. We finish fixing the factory and then go back to the beginning. This continues until we achieve perfection.
It is important to understand how to measure the effectiveness and implementation of kaizen in your company. There are many ways to tell if kaizen is effective. One method is to inspect the finished products for defects. Another method is to determine how much productivity has improved since the implementation of kaizen.
A good way to determine whether kaizen has been implemented is to ask why. You were trying to save money or obey the law? It was a way to save money or help you succeed.
Congratulations if you answered "yes" to any of the questions. You are now ready to begin kaizen.