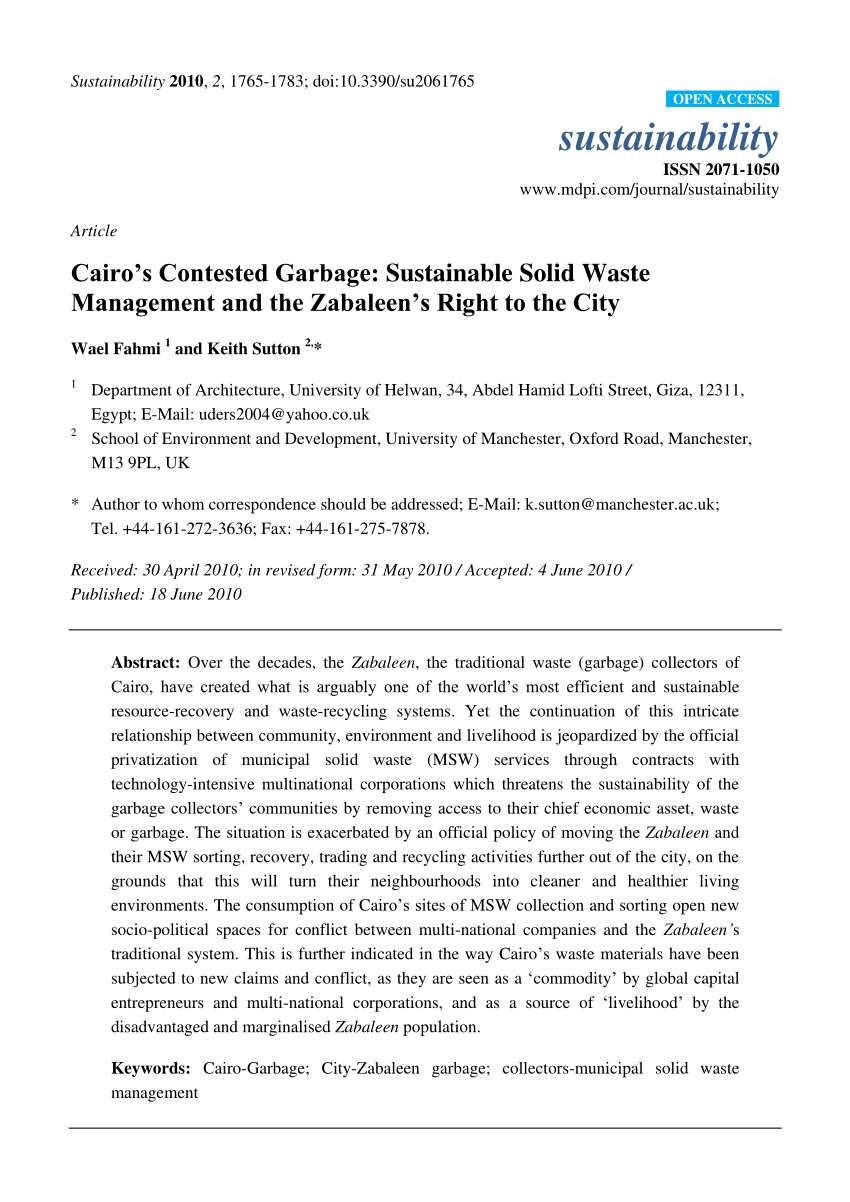
Behaviour based safety (BBS), is a way to improve safety. It applies the science behind behaviour change to real-world safety problems. This creates safety partnerships between management and employees by focusing attention on everyday safety behavior. The goal is to make work safer.
Safety based on behaviour
Behaviour-Based Safety is a process that encourages employees to make changes to improve safety. This includes gathering safety behaviour data and redesigning work processes to implement safer work practices. Finally, the system is tested for its effectiveness. Behaviour-Based Safety is a dynamic process and changes over time as more is learned. In this example, the initial model may not be viable after a few months. BBS programs, which are often complex, require a change management plan, training, and other variables.
A comprehensive safety program should encompass a range of activities and topics. It should encourage employees and motivate them to take control of their safety. Many employees are responsible for injuries or other incidents that result from their actions. Employees can be injured or even killed by their actions. A good safety program must address both high risk and low risk behaviors.
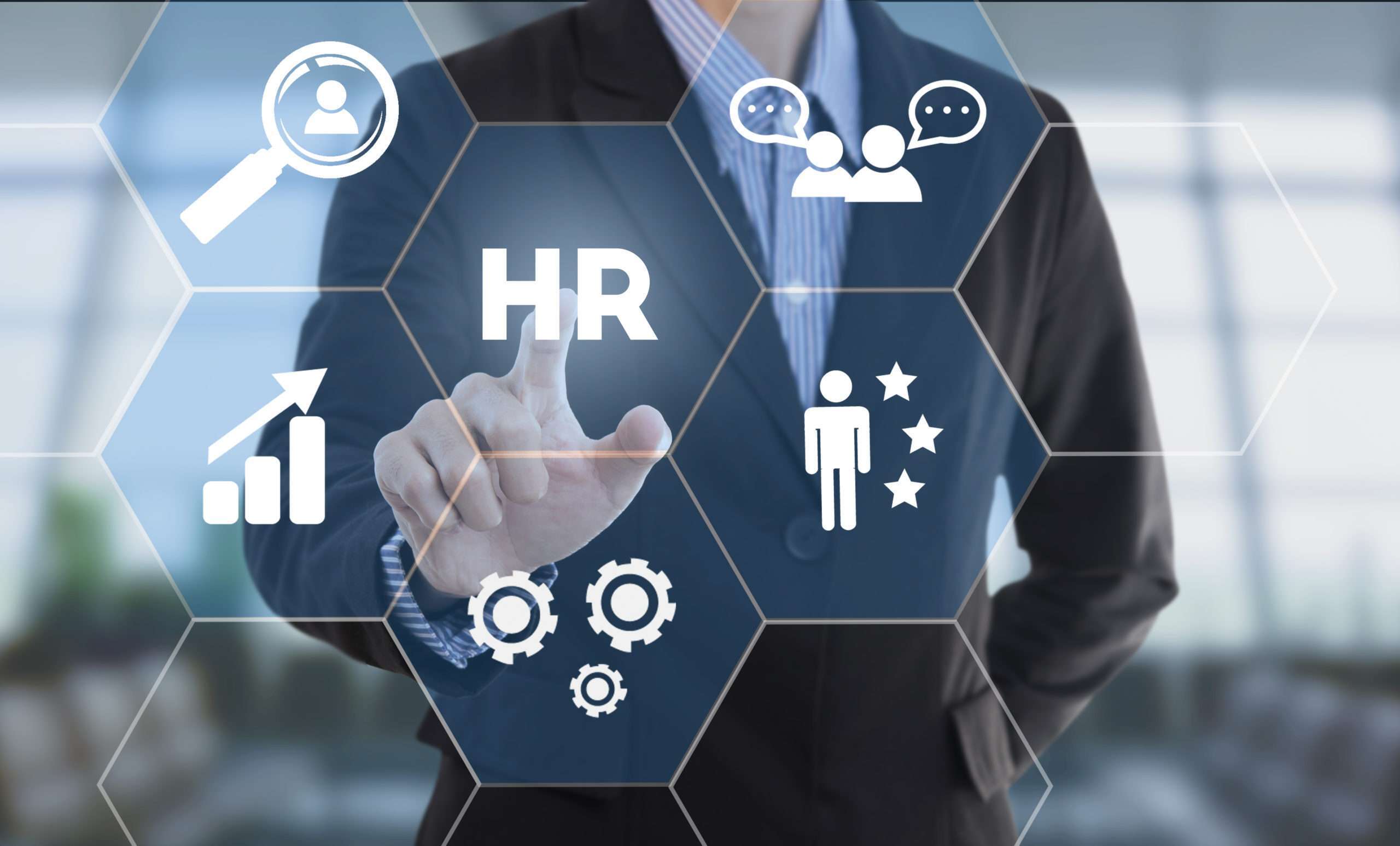
Behaviour-Based Safety Culture
To improve safety performance, a behaviour-based safety environment can be implemented. Not only can it reduce accident rates, it can also reduce the risk of near misses and potential incidents. Resistance to change can make it difficult to implement this approach. However, investing in a behaviour-based safety culture will help people respond in the right way in critical situations. This can provide long-term benefits for the company.
Along with training employees how to behave in a safe workplace environment, safety-based culture should also include a list of policies. These policies should give an overview of the company's safety approach and include ways to improve it. These policies should also contain regular safety training for all employees.
Behaviour-based safety system for measuring
A Behaviour-based system of measure measures safety performance in the workplace. This system of measurement helps identify the key workplace behaviours. It then designs an effective prevention or control program. It also helps make a solid business case for solutions that will prevent and control workplace accidents and injuries.
Behavioral safety checks are often done every day, weekly or monthly. They should keep track of both risky and good behaviours, and highlight areas that need improvement.
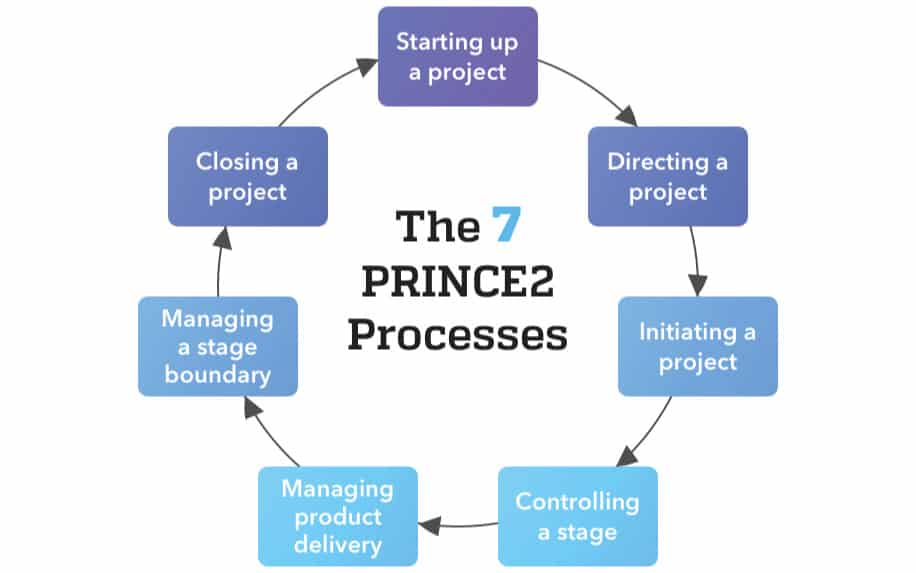
Benefits of the BBS program
BBS programs can be a great way to improve safety culture at work. The program can be used by employees to hold each other accountable for any unsafe behavior. BBS helps to prevent accidents and improves the health of employees. It can prevent illness and injury from hazardous substances.
You must set clear goals to make your program successful. The goals can be as simple as reducing the number and severity of near-misses each year. Or increasing the percentage of employees who are wearing PPE. Also, you should set goals that are both achievable and manageable to discourage employees. Additionally, you need a plan that will guide the implementation of the program.
FAQ
What are the main four functions of management
Management is responsible in planning, organizing and directing people and resources. Management also involves setting goals and developing policies.
Organizations can achieve their goals through management. This includes leadership, coordination, control and motivation.
The following are the four core functions of management
Planning - Planning involves determining what needs to be done.
Organizing – Organizing means deciding how to organize things.
Directing - This refers to getting people follow instructions.
Controlling - This is the ability to control people and ensure that they do their jobs according to plan.
What is a simple management tool that aids in decision-making and decision making?
A decision matrix can be a simple, but effective tool to assist managers in making decisions. They can think about all options and make informed decisions.
A decision matrix is a way to organize alternatives into rows and columns. This allows you to easily see how each choice affects others.
This example shows four options, each represented by the boxes on either side of the matrix. Each box represents one option. The top row represents the current state of affairs, and the bottom row is indicative of what would happen in the event that nothing were done.
The effect of selecting Option 1 is shown in the middle column. In this example, it would lead to an increase in sales of between $2 million and $3 million.
The next two columns show the effects of choosing Options 2 and 3. These are positive changes - they increase sales by $1 million and $500 thousand respectively. These changes can also have negative effects. For instance, Option 2 increases cost by $100 thousand while Option 3 reduces profits by $200 thousand.
The final column shows the results for Option 4. This means that sales will decrease by $1 million.
The best part of using a decision-matrix is that it doesn't require you to know which numbers belong where. The best thing about a decision matrix is that you can simply look at the cells, and immediately know whether one option is better or not.
The matrix has already done all of the work. It is as simple as comparing the numbers within the relevant cells.
Here's an example showing how you might use a Decision Matrix in your business.
Decide whether you want to invest more in advertising. If you do, you'll be able to increase your revenue by $5 thousand per month. However, additional expenses of $10 000 per month will be incurred.
The net result of advertising investment can be calculated by looking at the cell below that reads "Advertising." It is 15 thousand. Advertising is worth much more than the investment cost.
What kind people use Six Sigma?
Six Sigma is well-known to those who have worked in operations research and statistics. It can be used by anyone in any business aspect.
It requires high levels of commitment and leadership skills to be successful.
What is TQM exactly?
The quality movement was born during the industrial revolution when manufacturing companies realized they could not compete on price alone. To remain competitive, they had to improve quality as well as efficiency.
Management developed Total Quality Management to address the need for improvement. It focused on all aspects of an organisation's performance. It included continuous improvement, employee involvement and customer satisfaction.
What role does a manager play in a company?
Different industries have different roles for managers.
A manager generally manages the day to-day operations in a company.
He/she ensures that the company meets its financial obligations and produces goods or services that customers want.
He/she is responsible for ensuring that employees comply with all regulations and follow quality standards.
He/she designs new products or services and manages marketing campaigns.
Statistics
- Hire the top business lawyers and save up to 60% on legal fees (upcounsel.com)
- Your choice in Step 5 may very likely be the same or similar to the alternative you placed at the top of your list at the end of Step 4. (umassd.edu)
- The average salary for financial advisors in 2021 is around $60,000 per year, with the top 10% of the profession making more than $111,000 per year. (wgu.edu)
- 100% of the courses are offered online, and no campus visits are required — a big time-saver for you. (online.uc.edu)
- This field is expected to grow about 7% by 2028, a bit faster than the national average for job growth. (wgu.edu)
External Links
How To
How can Lean Manufacturing be done?
Lean Manufacturing methods are used to reduce waste through structured processes. They were created by Toyota Motor Corporation in Japan in the 1980s. It was designed to produce high-quality products at lower prices while maintaining their quality. Lean manufacturing seeks to eliminate unnecessary steps and activities in the production process. It is composed of five fundamental elements: continuous improvement; pull systems, continuous improvements, just-in–time, kaizen, continuous change, and 5S. Pull systems allow customers to get exactly what they want without having to do extra work. Continuous improvement refers to continuously improving existing processes. Just-in-time is when components and other materials are delivered at their destination in a timely manner. Kaizen means continuous improvement. Kaizen involves making small changes and improving continuously. Fifth, the 5S stand for sort, set up in order to shine, standardize, maintain, and standardize. These five elements work together to produce the best results.
Lean Production System
The lean production system is based on six key concepts:
-
Flow - The focus is on moving information and material as close as possible to customers.
-
Value stream mapping - break down each stage of a process into discrete tasks and create a flowchart of the entire process;
-
Five S's: Sort, Shine Standardize, Sustain, Set In Order, Shine and Shine
-
Kanban - use visual signals such as colored tape, stickers, or other visual cues to keep track of inventory;
-
Theory of constraints - identify bottlenecks during the process and eliminate them with lean tools like Kanban boards.
-
Just-intime - Order components and materials at your location right on the spot.
-
Continuous improvement is making incremental improvements to your process, rather than trying to overhaul it all at once.