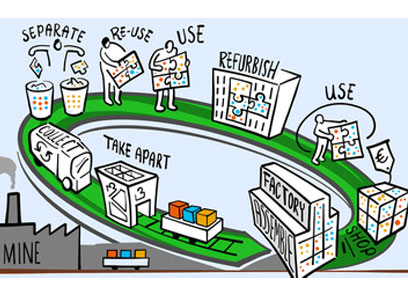
Project managers spend a lot of time communicating with stakeholders and leading others. Their success is dependent on their leadership skills. They also need to have a number of technical skills. These are Time management, Planning, Strategic management, and Quality management. These skills will make it easier to manage projects.
Time management
Project managers must learn time management to maximize productivity and ensure projects are completed on-time. To effectively organize a project into tasks and/or sub-tasks and assign a time limit to each task or group of sub-tasks groups, it is essential to master time management. A variety of management techniques and tools can be used to practice this skill.
It is essential to manage your time because you can accomplish more with less time. It can also help you avoid stress and overload. You must make sure you have enough time to complete each task so that you can concentrate on them. You'll be able finish your project on-time and with less strain.
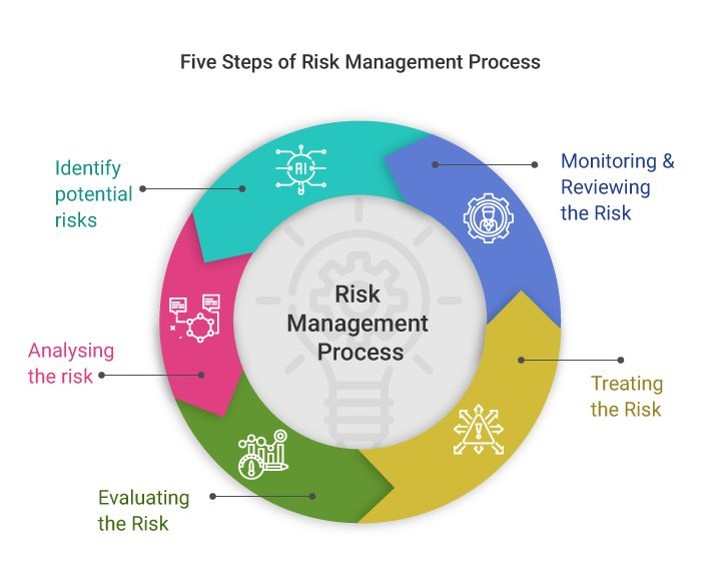
Planning
Planning is an important aspect of a project. To be successful, a project manager must possess specific technical skills. Project managers need to be able to understand the timelines and budgets of projects and balance cost and scope. Strong writing and reading skills are essential. These skills are important for many careers, but are especially relevant in project management. Managers of projects often need to be able to read technical documents and translate them into briefs.
Project managers should also be able and able to plan for resources. This includes planning and organizing resources, scheduling, and justifying expenses. Other important skills include problem solving, team motivation, and negotiation skills.
Strategic management
Strategic management is the ability to plan and execute the results of a project. It involves creating a strategy plan and then executing it in order to achieve the desired outcome. It also involves the ability to assess the execution and communication of a plan. You must be able to adapt to change, and to continuously improve your strategic management skills.
To be able successfully manage and control projects, project managers need to master strategic management. They must have a deep understanding of the business strategy and its relationship to project objectives. This connection is crucial to avoid projects going off-track or failing.
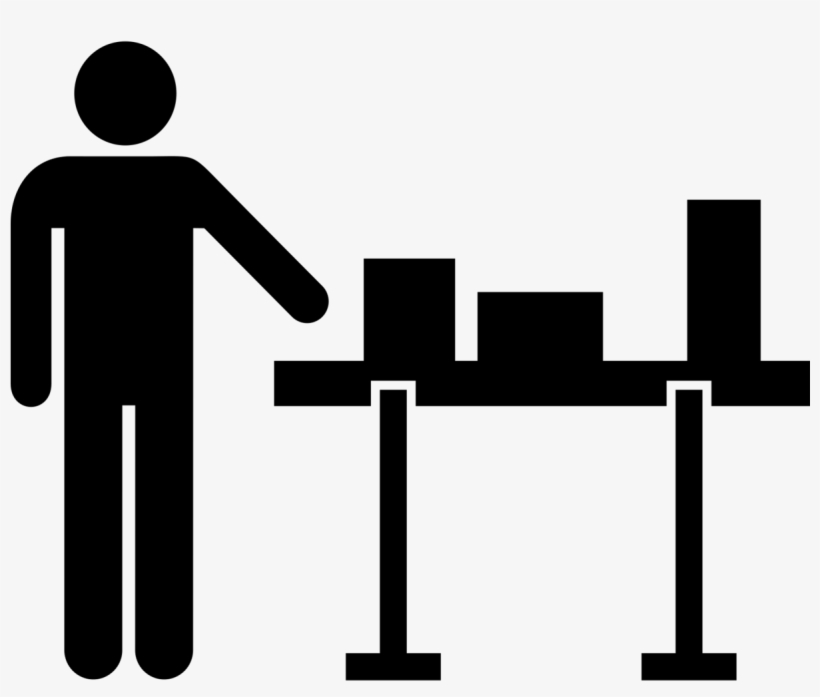
Management quality
The Quality Manager's job is to ensure that the project goes as smoothly as possible. This involves being able to communicate with the team and ensure that they know exactly what their responsibilities are. It also means being able to communicate the challenges and the performance criteria for the project.
Also, project managers need to be problem-solving and analytical. They must be able to work with a diverse team, and they must be able to communicate with all project stakeholders effectively. They must be able and able to develop effective project schedules. This skill is lacking in many project managers.
FAQ
Which kind of people use Six Sigma
Six Sigma will most likely be familiar to people who have worked in statistics and operations research. However, anyone involved in any aspect of business can benefit from using it.
Because it requires a high level of commitment, only those with strong leadership skills will make an effort necessary to implement it successfully.
What is Six Sigma?
It's a strategy for quality improvement that emphasizes customer care and continuous learning. The objective is to eliminate all defects through statistical methods.
Six Sigma was developed at Motorola in 1986 as part of its efforts to improve manufacturing processes.
It was quickly adopted by the industry and many companies are now using six-sigma to improve product design, production, delivery, customer service, and product design.
What is Kaizen?
Kaizen is a Japanese term meaning "continuous improvement." It is a philosophy that encourages employees to constantly look for ways to improve their work environment.
Kaizen is a belief that everyone should have the ability to do their job well.
What are some common management mistakes?
Managers sometimes make their own job harder than necessary.
They might not give enough support and delegate the right responsibilities to their staff.
Managers often lack the communication skills necessary to motivate and guide their teams.
Managers set unrealistic expectations and make it difficult for their team.
Managers may prefer to solve every problem for themselves than to delegate responsibility.
Statistics
- The profession is expected to grow 7% by 2028, a bit faster than the national average. (wgu.edu)
- The average salary for financial advisors in 2021 is around $60,000 per year, with the top 10% of the profession making more than $111,000 per year. (wgu.edu)
- The BLS says that financial services jobs like banking are expected to grow 4% by 2030, about as fast as the national average. (wgu.edu)
- Your choice in Step 5 may very likely be the same or similar to the alternative you placed at the top of your list at the end of Step 4. (umassd.edu)
- UpCounsel accepts only the top 5 percent of lawyers on its site. (upcounsel.com)
External Links
How To
How is Lean Manufacturing done?
Lean Manufacturing is a method to reduce waste and increase efficiency using structured methods. These processes were created by Toyota Motor Corporation, Japan in the 1980s. The goal was to produce quality products at lower cost. Lean manufacturing seeks to eliminate unnecessary steps and activities in the production process. It is made up of five elements: continuous improvement, continuous improvement, just in-time, continuous change, and 5S. Pull systems are able to produce exactly what the customer requires without extra work. Continuous improvement is the continuous improvement of existing processes. Just-in-time is when components and other materials are delivered at their destination in a timely manner. Kaizen means continuous improvement. Kaizen involves making small changes and improving continuously. Fifth, the 5S stand for sort, set up in order to shine, standardize, maintain, and standardize. These five elements can be combined to achieve the best possible results.
Lean Production System
Six key concepts underlie the lean production system.
-
Flow is about moving material and information as near as customers can.
-
Value stream mapping: This is a way to break down each stage into separate tasks and create a flowchart for the entire process.
-
Five S's - Sort, Set In Order, Shine, Standardize, and Sustain;
-
Kanban is a visual system that uses visual cues like stickers, colored tape or stickers to keep track and monitor inventory.
-
Theory of constraints - identify bottlenecks during the process and eliminate them with lean tools like Kanban boards.
-
Just-in time - Get components and materials delivered right at the point of usage;
-
Continuous improvement - make incremental improvements to the process rather than overhauling it all at once.