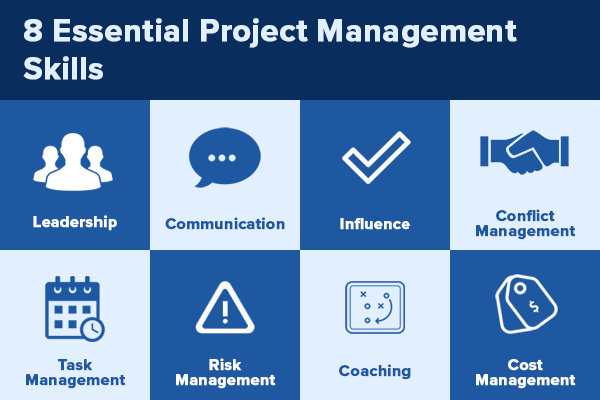
A supply-chain management certificate might be a good idea if your goal is to get into supply chain administration. This program can teach you how to effectively manage the flow of goods throughout the entire supply chain. This certificate program also helps you develop your professional skills and knowledge. After you graduate, you can begin a career as a logistics analyst, transportation manager, or purchasing professional. If you're looking for a job that is both fast-paced and involves extensive travel, this program can prove to be very rewarding.
Certification vs. supply-chain management certificate
The Supply Chain Management Certificate online program provides training in supply chain management. Students are able to choose from courses that focus on a broad spectrum of topics, or specialize in specific areas of interest. The certificate is designed for managers in different departments such as purchasing, operations and production. It equips students with the knowledge and skills needed to succeed in this industry. Courses in the curriculum teach students how to balance inventory costs and analyze key performance indicator.
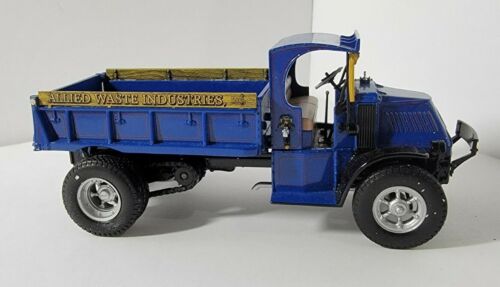
Students must complete four courses as introductory and one capstone course on supply chain strategy to earn the Supply Chain Management Certificate. Students are required to complete a real-world business case during the program, which requires practical application of the knowledge gained. This program is ideal for students just starting out in the industry. The schedule is flexible. A minimum of three hours is required per week.
Curriculum for supply chain management certificate
A Supply Chain Management Certificate is an excellent way to improve your skills and knowledge. You will be able to focus your research on certain areas. This certificate is designed to train students in managing the supply chain from start to finish. The curriculum is intended for supply chain managers and executives interested in implementing supply-chain management strategies and practices in their business. The certificate requires 31 credits. The certificate focuses on a few key areas.
You must take the following courses to earn your Supply Chain Management Certificate. SCM 384 is a course that introduces supply-chain management. SCM 334 and SCM 381 are available. SCM 380 can be taken anytime, which is enterprise resource planning. These courses provide the foundation for your certificate. You must complete them before starting your program.
Programs that offer supply chain management certificates
There are many online programs that offer certificates in supply chain management. These certificates can help you develop the skills that employers will value most. Students also get to use the coursework in practice. Towson University has a graduate certificate program in supply chain management which can give you an edge in your chosen field. The university offers a flexible evening schedule that makes it possible to complete the program in a year.
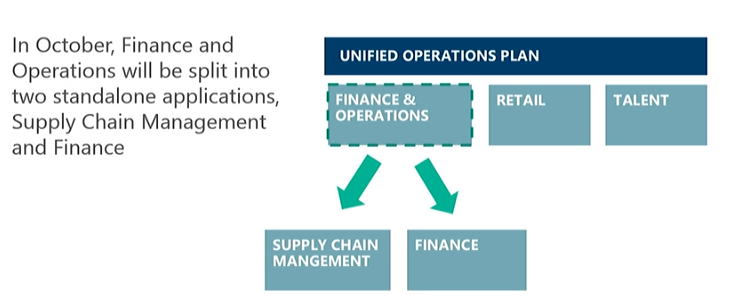
18 credits of coursework are required in order to obtain a supply management certificate. There are four required courses, and two electives. Six Sigma Quality Management or International Supply Chain Management are two options for electives. Internships in operations/project administration are also available. These can be a great source of hands-on experience that will open up new possibilities and provide valuable insight. An internship in retail or manufacturing is required to earn your certificate.
FAQ
How can a manager enhance his/her leadership skills?
You can improve your management skills by practicing them at all times.
Managers must continuously monitor the performance levels of their subordinates.
If you notice your subordinate isn't performing up to par, you must take action quickly.
It is important to be able identify areas that need improvement and what can be done to improve them.
How do you manage your employees effectively?
The key to effective management of employees is ensuring their happiness and productivity.
It also means having clear expectations of their behavior and keeping track of their performance.
Managers must be clear about their goals and those of their teams in order to succeed.
They should communicate clearly to staff members. And they need to ensure that they reward good performance and discipline poor performers.
They must also keep records of team activities. These include:
-
What was achieved?
-
How much work was done?
-
Who did it, anyway?
-
How did it get done?
-
Why did it happen?
This information can help you monitor your performance and to evaluate your results.
How does Six Sigma work
Six Sigma uses statistical analyses to locate problems, measure them, analyze root cause, fix problems and learn from the experience.
The first step is to identify the problem.
Next, data are collected and analyzed in order to identify patterns and trends.
Then corrective actions are taken to solve the problem.
Finally, the data are reanalyzed in order to determine if it has been resolved.
This continues until the problem has been solved.
What are the key management skills?
No matter if they are running a local business or an international one, management skills are vital. These include the ability and willingness to manage people, finances as well resources, time and space.
When you need to manage people, set goals, lead teams, motivate them, solve problems, develop policies and procedures and manage change, management skills are essential.
There are so many managerial tasks!
What is the difference between leadership and management?
Leadership is about influencing others. Management is about controlling others.
A leader inspires his followers while a manager directs the workers.
A leader motivates people and keeps them on task.
A leader develops people; a manager manages people.
How can we create a culture of success in our company?
A positive company culture creates a sense of belonging and respect in its people.
It's founded on three principal principles:
-
Everybody has something of value to share
-
Fair treatment of people is the goal
-
There is mutual respect between individuals and groups
These values can be seen in the behavior of people. They will treat others with respect and kindness.
They will respect the opinions of others.
They encourage others to express their feelings and ideas.
Company culture also encourages open communication, collaboration, and cooperation.
People feel free to express their views openly without fear of reprisal.
They understand that mistakes can be forgiven as long as they're dealt with honestly.
The company culture encourages honesty and integrity.
Everyone knows that they must always tell truth.
Everyone understands that there are rules and regulations which apply to them.
People don't expect special treatment or favors.
Statistics
- Hire the top business lawyers and save up to 60% on legal fees (upcounsel.com)
- 100% of the courses are offered online, and no campus visits are required — a big time-saver for you. (online.uc.edu)
- The profession is expected to grow 7% by 2028, a bit faster than the national average. (wgu.edu)
- This field is expected to grow about 7% by 2028, a bit faster than the national average for job growth. (wgu.edu)
- As of 2020, personal bankers or tellers make an average of $32,620 per year, according to the BLS. (wgu.edu)
External Links
How To
How do I do the Kaizen Method?
Kaizen means continuous improvement. This Japanese term refers to the Japanese philosophy of continuous improvement that emphasizes incremental improvements and constant improvement. It is a process where people come together to improve their processes.
Kaizen is one of Lean Manufacturing's most efficient methods. This concept requires employees to identify and solve problems during manufacturing before they become major issues. This increases the quality of products and reduces the cost.
Kaizen is about making everyone aware of the world around them. Correct any errors immediately to avoid future problems. If someone is aware of a problem at work, he/she should inform his/her manager immediately.
When doing kaizen, there are some principles we must follow. We always start from the end product and move toward the beginning. We can improve the factory by first fixing the machines that make it. Next, we fix the machines which produce components. We then fix the workers that work with those machines.
This method is known as kaizen because it focuses upon improving every aspect of the process step by step. Once we have finished fixing the factory, we return to the beginning and work until perfection.
How to measure kaizen's effectiveness in your business is essential to implement it. There are several ways to determine whether kaizen is working well. One of these ways is to check the number of defects found on the finished products. Another way is determining how much productivity increased after implementing kaizen.
Another way to know whether kaizen is working is to ask yourself why did you decide to implement kaizen. Did you do it because it was legal or to save money? You really believed it would make you successful?
Suppose you answered yes to any of these questions, congratulations! You are now ready to begin kaizen.