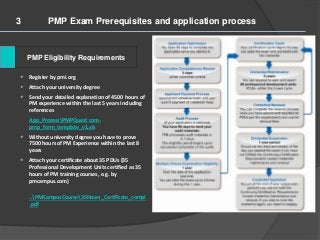
This article will focus on the main activities of the value chain. These activities involve the supply of raw materials to a firm, the production and sale of these materials, and the management of employees. All of these activities are essential to any business. These sections will provide more information about each activity. These activities can be understood better if you look at the definitions. In the value chain, procurement is the acquisition of raw materials, such as oil, metal, and wood, for a firm.
Operation
The operations phase of the value chain relates to changing inputs into finished products. It is often equated with production, especially in industries that produce physical goods. However, it can also apply to services. A typical example of an operation phase is the need to use raw materials and labor in order to produce a finished item. For a service-based firm, operations might include managing inventory and providing administrative support. The primary objective of this phase is to create value.
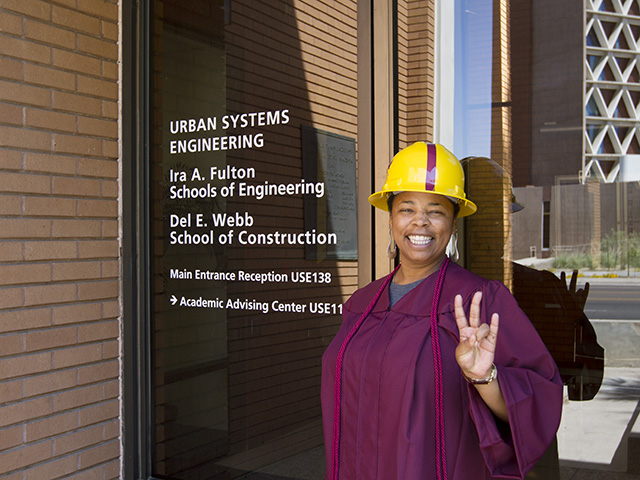
Sales
Sales is one of the primary activities in a value chain. It involves both the selling and purchasing of a product. A company develops, markets, and closes sales. All of these activities can be referred to as the value chain. It is crucial that a company succeeds in sales and marketing. They are critical for a company to grow its market, revenue, profits, and market value. The value chain assessment will be made easier by identifying each activity and the raw materials.
Marketing
After-sales support is essential for any company's promotion and marketing efforts. Customers have the ability to express their dissatisfaction online. It is important that companies have proper after-sales support practices. These activities include product adjustment, repair, training, part supply, installation and repair.
Distribution
Distribution of goods, and services, is one of the key activities of a value chains. The value of a service or good can be affected by many factors. One factor is the cost. Consumers will often pay more for finished goods than raw materials. Innovations and unique items can improve a company's perceived value. This perception can have a major impact on the margins and profitability of a product.
Infrastructure
As the foundation of a value chain, infrastructure involves processes that support the top-level business decisions, including finance, compliance, and quality control. An effective strategic infrastructure integrates these activities and provides coordination that allows for efficient management of all aspects. These are some examples for strategic infrastructure. Investing in it can lead to competitive advantage. Strategic infrastructure is not only important for financial management but it can also be used to reduce technology costs.
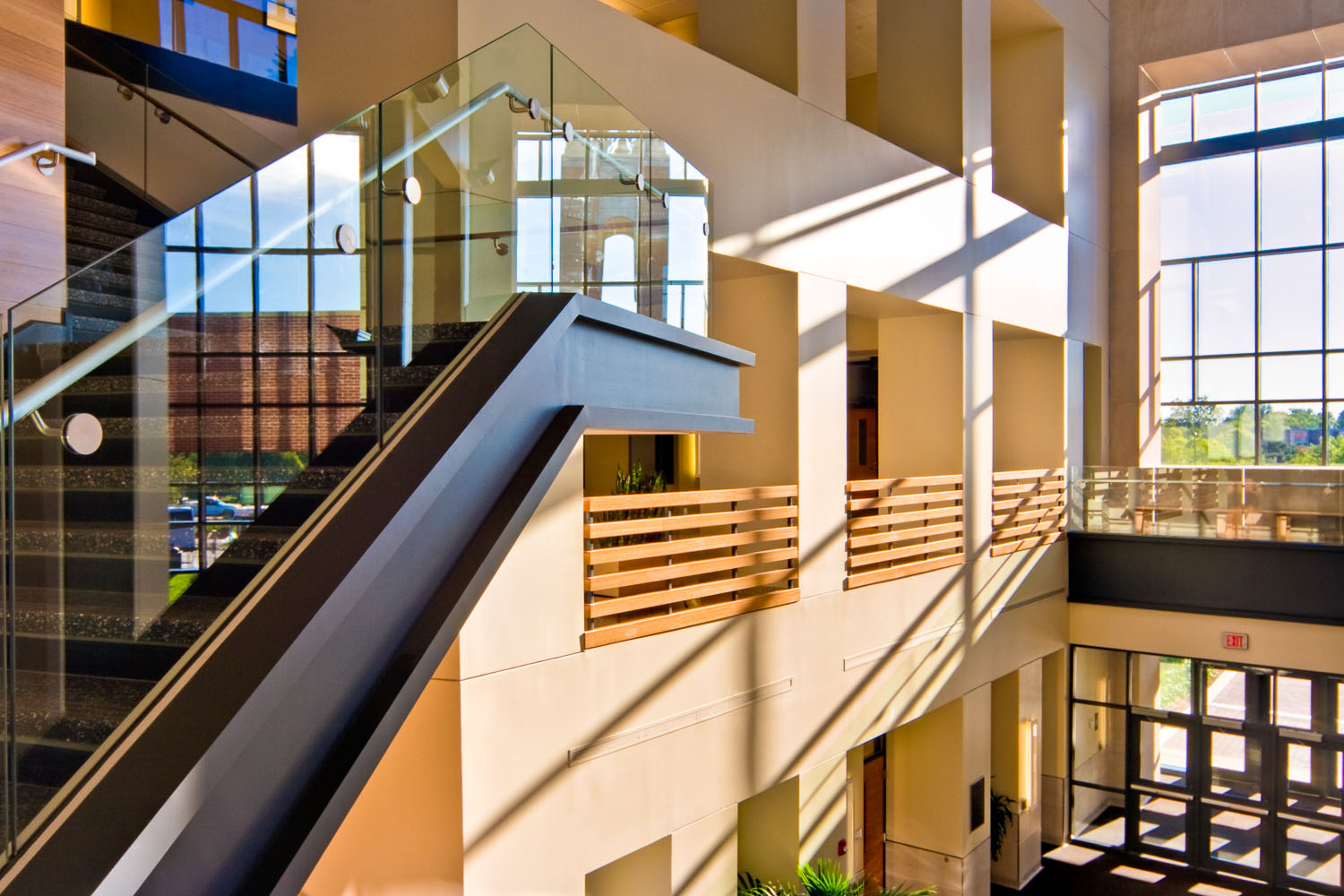
Customer service
Customer care is just as important in customer service as the promotion of your products. You can be certain that if a customer is unhappy with your product or service, the feedback will spread quickly and can have serious consequences. Companies must have the right customer service policies. After-sales service activities can include repair, installation, and product adjustments.
FAQ
How do you define Six Sigma?
People who have worked with statistics and operations research will usually be familiar with the concepts behind six sigma. Anybody involved in any aspect or business can benefit.
Because it requires a high degree of commitment, only leaders with strong leadership skills can implement it successfully.
How does Six Sigma work?
Six Sigma employs statistical analysis to identify problems, measure them and analyze root causes. Six Sigma also uses experience to correct problems.
The first step is to identify the problem.
Next, data is collected and analyzed to identify trends and patterns.
The problem is then rectified.
Finally, data will be reanalyzed to determine if there is an issue.
This cycle will continue until the problem is solved.
What is the difference between TQM and Six Sigma?
The main difference between these two quality management tools is that six sigma focuses on eliminating defects while total quality management (TQM) focuses on improving processes and reducing costs.
Six Sigma is a method for continuous improvement. It emphasizes the elimination and improvement of defects using statistical methods, such as control charts, P-charts and Pareto analysis.
The goal of this method is to reduce variation in product output. This is done by identifying root causes and rectifying them.
Total quality management is the measurement and monitoring of all aspects within an organization. This includes training employees to improve their performance.
It is often used as a strategy to increase productivity.
What role should a manager play within a company
The role of a manager varies from one industry to another.
The manager oversees the day-to-day activities of a company.
He/she ensures the company meets its financial commitments and produces goods/services that customers demand.
He/she ensures employees adhere to all regulations and quality standards.
He/she plans and oversees marketing campaigns.
What is Kaizen, exactly?
Kaizen is a Japanese term which means "continuous improvement." This philosophy encourages employees to continually look for ways to improve the work environment.
Kaizen is based on the belief that every person should be able to do his or her job well.
Statistics
- 100% of the courses are offered online, and no campus visits are required — a big time-saver for you. (online.uc.edu)
- Hire the top business lawyers and save up to 60% on legal fees (upcounsel.com)
- The BLS says that financial services jobs like banking are expected to grow 4% by 2030, about as fast as the national average. (wgu.edu)
- This field is expected to grow about 7% by 2028, a bit faster than the national average for job growth. (wgu.edu)
- Your choice in Step 5 may very likely be the same or similar to the alternative you placed at the top of your list at the end of Step 4. (umassd.edu)
External Links
How To
How does Lean Manufacturing work?
Lean Manufacturing processes are used to reduce waste and improve efficiency through structured methods. They were developed in Japan by Toyota Motor Corporation (in the 1980s). The goal was to produce quality products at lower cost. Lean manufacturing is about eliminating redundant steps and activities from the manufacturing process. It is made up of five elements: continuous improvement, continuous improvement, just in-time, continuous change, and 5S. It is a system that produces only the product the customer requests without additional work. Continuous improvement involves constantly improving upon existing processes. Just-in–time refers when components or materials are delivered immediately to their intended destination. Kaizen stands for continuous improvement. Kaizen can be described as a process of making small improvements continuously. Last but not least, 5S is for sort. To achieve the best results, these five elements must be used together.
Lean Production System
Six key concepts make up the lean manufacturing system.
-
Flow is about moving material and information as near as customers can.
-
Value stream mapping- This allows you to break down each step of a process and create a flowchart detailing the entire process.
-
Five S's – Sort, Put In Order Shine, Standardize and Sustain
-
Kanban – visual signals like colored tape, stickers or other visual cues are used to keep track inventory.
-
Theory of constraints: identify bottlenecks in your process and eliminate them using lean tools, such as kanban board.
-
Just-intime - Order components and materials at your location right on the spot.
-
Continuous improvement - incremental improvements are made to the process, not a complete overhaul.