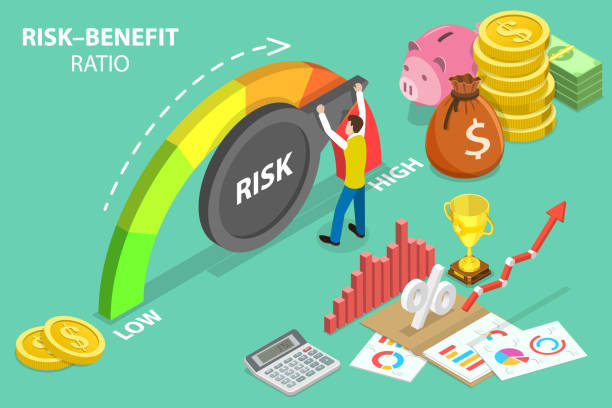
The waste hierarchy is a tool used to evaluate environmental actions. It ranks the most environmentally-beneficial actions and identifies priority programs based upon sustainability. The waste hierarchy is a valuable tool in addressing waste management. It can be applied to many aspects of environmental control, including the production and use of food, water, or energy.
Prevent
Prevent waste hierarchy is about preventing waste from the source. Avoiding products with excessive packaging is one way to reduce waste. This is the first step towards reducing waste. To do this, you need to understand how waste materials are manufactured, packaged, and disposed. In addition, businesses should aim to reduce their consumption of perishable goods and prepare their waste for reuse.
The waste hierarchy can help companies and consumers promote circular economy and sustainability. It will allow them to reduce the amount of waste they produce, discourage the production of unneeded products, and encourage the development green technologies to reduce harmful greenhouse gas emissions.
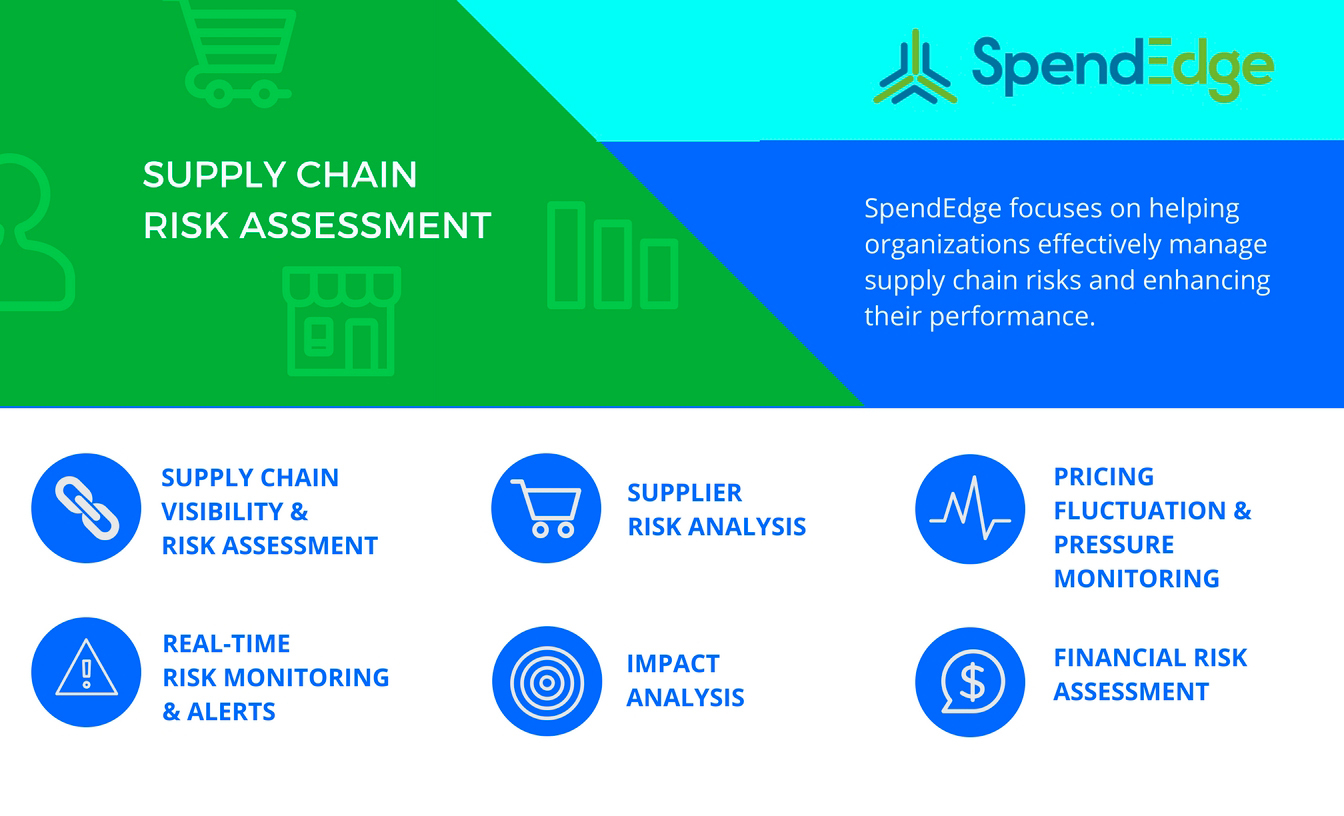
Recycle
The waste hierarchy is an environmental evaluation tool that ranks different actions by their environmental benefits. It is used in determining program priorities. It ranks actions from the most favorable to the least favorable. A waste hierarchy shows the best and worst ways of achieving desired results. This hierarchy can be used to determine the most efficient program practices.
The first stage of the hierarchy is prevention, which entails minimizing waste generation. Next, the reuse stage focuses on recovering valuable material. The most dangerous step of all is disposal.
Do not dispose
Although there are many ways of disposing of waste, one of the best methods is the waste hierarchy. This system allows for reuse, recycling, and re-using of waste materials. Some waste materials cannot be recycled or reused and may need to be treated before they can safely be disposed of.
A waste hierarchy is a tool that helps decision-makers decide which waste management practices will produce the most positive impact on the environment. The waste hierarchy has five stages. The first stage is prevention. Next, there are recovery, disposal, and preparation.
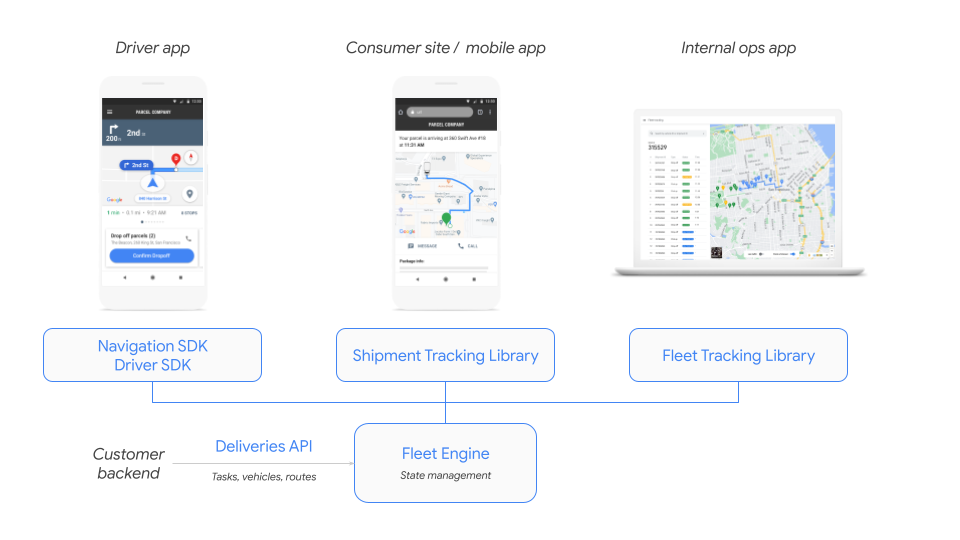
Prevention
The Prevention of Waste Hierarchy is the key for reducing waste and protecting nature. The hierarchy has different levels, each with different environmental impacts. The first level is Reduction, where waste is reduced by using less materials or avoiding materials that have negative environmental effects. Prevention is the second level. It involves streamlining product design and encouraging long-term product use. Prevention also includes research and development of cleaner technologies.
The prevention of waste hierarchy identifies different methods for reducing waste and ensuring its safe and effective management. It is currently part of recycling regulations and solid-waste management plans. It also includes recovery prior to disposal. Many organizations tend to focus on the fourth R when they should be focusing on the first two. This can lead to costly systems that don’t reduce waste and have adverse environmental impacts. Zero Waste International Alliance adopted the world's only peer-reviewed Zero Waste Hierarchy. This promotes the three main methods of waste reduction.
FAQ
What is the main difference between Six Sigma Six Sigma TQM and Six Sigma Six Sigma?
The main difference between these two quality management tools is that six sigma focuses on eliminating defects while total quality management (TQM) focuses on improving processes and reducing costs.
Six Sigma is a methodology for continuous improvement. It emphasizes the elimination and improvement of defects using statistical methods, such as control charts, P-charts and Pareto analysis.
This method has the goal to reduce variation of product output. This is accomplished by identifying the root cause of problems and fixing them.
Total quality management refers to the monitoring and measurement of all aspects in an organization. It also involves training employees to improve performance.
It is frequently used as an approach to increasing productivity.
What is TQM?
The industrial revolution led to the birth and growth of the quality movement. Manufacturing companies realized they couldn't compete solely on price. They needed to improve the quality and efficiency of their products if they were to be competitive.
To address this need for improvement management created Total Quality Management (TQM) which aimed to improve all aspects of an organization's performance. It involved continuous improvement, employee participation, and customer satisfaction.
What are the steps in the decision-making process in management?
The decision-making process of managers is complicated and multifaceted. It involves many elements, including analysis, strategy. planning. implementation. measurement. evaluation. feedback.
The key thing to remember when managing people is that they are human beings just as you are and therefore make mistakes. You are always capable of improving yourself, and there's always room for improvement.
This video will explain how decision-making works in Management. We discuss different types of decisions as well as why they are important and how managers can navigate them. You'll learn about the following topics:
What is Six Sigma?
It's a strategy for quality improvement that emphasizes customer care and continuous learning. The objective is to eliminate all defects through statistical methods.
Motorola's 1986 efforts to improve manufacturing process efficiency led to the creation of Six Sigma.
The idea quickly spread in the industry. Many organizations today use six-sigma methods to improve product design and production, delivery and customer service.
What is the difference between management and leadership?
Leadership is all about influencing others. Management is all about controlling others.
A leader inspires others while a manager directs them.
A leader motivates people and keeps them on task.
A leader develops people; a manager manages people.
What is Kaizen, exactly?
Kaizen is a Japanese term for "continuous improvement." It encourages employees constantly to look for ways that they can improve their work environment.
Kaizen is based upon the belief that each person should be capable of doing his or her job well.
What are the main four functions of management
Management is responsible for organizing, managing, directing and controlling people, resources, and other activities. This includes setting goals, developing policies and procedures, and creating procedures.
Management helps an organization achieve its objectives by providing direction, coordination, control, leadership, motivation, supervision, training, and evaluation.
Management's four main functions are:
Planning - This is the process of deciding what should be done.
Organizing is the act of deciding how things should go.
Directing - Directing means getting people to follow instructions.
Controlling - This is the ability to control people and ensure that they do their jobs according to plan.
Statistics
- Hire the top business lawyers and save up to 60% on legal fees (upcounsel.com)
- Our program is 100% engineered for your success. (online.uc.edu)
- The profession is expected to grow 7% by 2028, a bit faster than the national average. (wgu.edu)
- The BLS says that financial services jobs like banking are expected to grow 4% by 2030, about as fast as the national average. (wgu.edu)
- 100% of the courses are offered online, and no campus visits are required — a big time-saver for you. (online.uc.edu)
External Links
How To
How do you apply the Kaizen method to your life?
Kaizen means continuous improvement. Kaizen is a Japanese concept that encourages constant improvement by small incremental changes. It is a process where people come together to improve their processes.
Kaizen is one the most important methods of Lean Manufacturing. Employees responsible for the production line should identify potential problems in the manufacturing process and work together to resolve them. This improves the quality of products, while reducing the cost.
Kaizen is about making everyone aware of the world around them. Correct any errors immediately to avoid future problems. If someone spots a problem while at work, they should immediately report it to their manager.
Kaizen has a set of basic principles that we all follow. We always start from the end product and move toward the beginning. We can improve the factory by first fixing the machines that make it. Next, we fix the machines which produce components. We then fix the workers that work with those machines.
This method, called 'kaizen', focuses on improving each and every step of the process. When we are done fixing the whole factory, we go back to the beginning and continue until we reach perfection.
It is important to understand how to measure the effectiveness and implementation of kaizen in your company. There are many methods to assess if kaizen works well. One method is to inspect the finished products for defects. Another way is to see how much productivity has increased since implementing kaizen.
To determine if kaizen is effective, you should ask yourself why you chose to implement kaizen. You were trying to save money or obey the law? Did you really believe that it would be a success factor?
Congratulations! Now you're ready for kaizen.