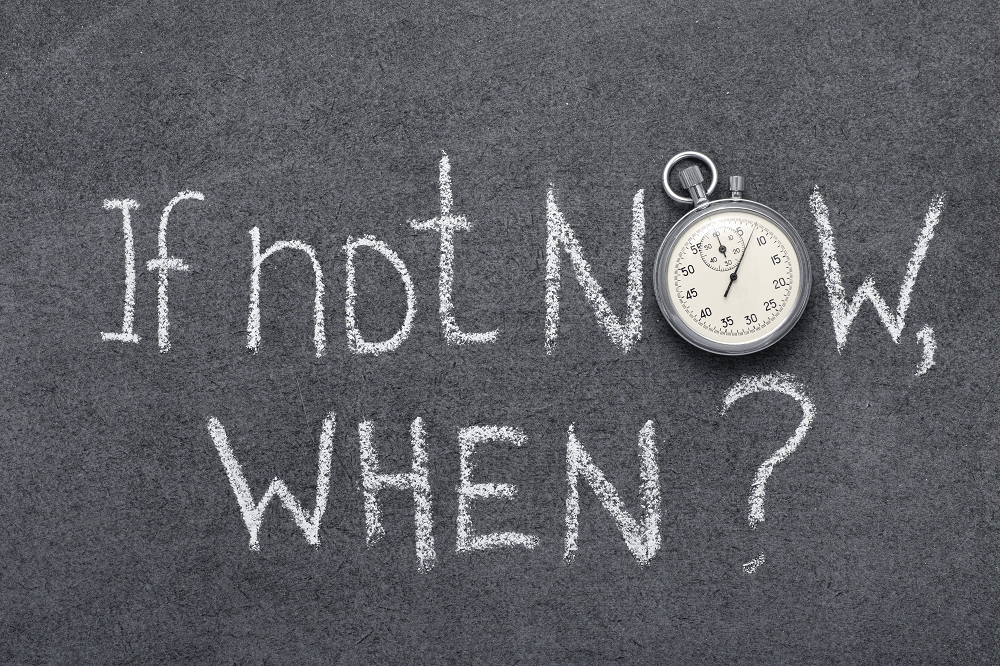
Some employees resist the idea of changing, but many are open to it. If you have ever managed a project that was met with resistance, don’t despair. There are many methods to overcome resistance to change, but first understand why it happens. The reasons for resistance vary greatly across different groups. These groups include employees, managers, stakeholders, and the external environment. If you want to increase employee engagement identify the root causes and then find solutions.
Employees
Employee resistance to change management can arise for many reasons. Some people will protest a change and attempt to stop its realization. Others might attempt to resist change through collective action like organizing labor unions or intentionally misinterpreting the direction. Whatever the reason, it is important to be aware of how to handle employee resistance to change management. These are some tips that will help you manage employee resistance positively.
Communicate effectively. Employees should be informed about changes to tools and processes when an organization adopts them. Then, the organization can ensure that the change will be successful by creating a learning culture for employees. This prevents employees from resisting change management. Employees must be provided with enough information, support and training to enable them to adapt to new tools and processes. The transition may be more difficult if employees aren't prepared. Management may have to return to the previous policy or process.
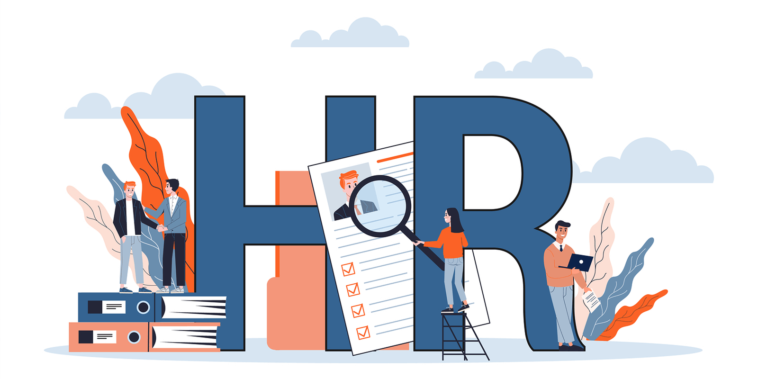
Managers
Managers need to convince workers that their changes are the best. In addition, they have to explain the changes' benefits. To reduce resistance to the changes, they should be gradually implemented. They should not pose a threat to worker security. Managers need to consider the opinions of all employees in order overcome resistance. Moreover, they should adapt to the changes by giving prior training to employees. They will eventually be able to accept the changes and reduce their resistance.
Employee resistance can be reduced by creating a positive environment where they feel valued. Employees will have a greater belief in the benefits of change and will resist management changes less. Employees will not feel informed about changes if they don't get it. Employees will also be less willing accept changes if they don't have the opportunity to participate in the changing process. If they aren't informed of the changes, they will have less faith in management.
Stakeholders
Change management resistance can have a major impact on the success and viability of an initiative. Developing an action plan for the change management effort can help you gain stakeholder buy-in and reduce stakeholder resistance. It is important that you recognize that not all stakeholders will resist change. Some stakeholders might simply be uncertain about the changes, while others may be more worried. It is important to inform stakeholders about the changes and to work with them to resolve any concerns.
While change can be difficult for everyone, it is often necessary in order to implement new initiatives. No matter the size of the change, stakeholders will want the opportunity to participate in it. Many employees are reluctant to accept change, and the organization needs to give them the power to participate in the change process. Software and other technological innovations can help you motivate and engage employees better. With the right tools, stakeholders can also self-engage in change management programs.
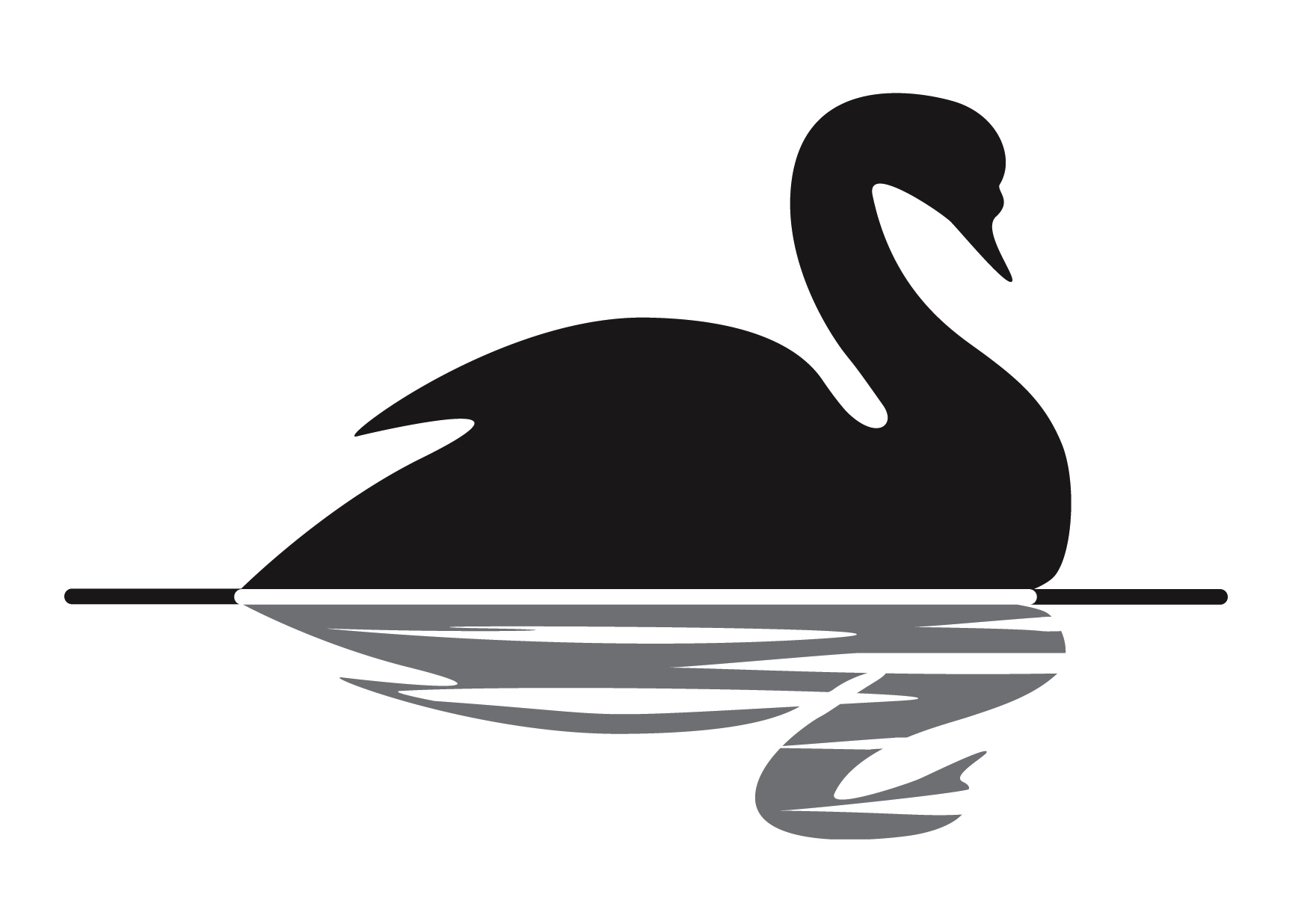
External environment
There are many reasons why people might resist change management. Some people will accept changes that make their lives better. This may be because they believe that these changes are positive. Others may resist change if they are afraid it will affect their career. However, it is important to recognize the different causes of resistance and take steps to minimize them. External environment can also cause resistance to change management.
Changes within an organization are bound to affect employees. Anxiety can be caused by new salespeople and job titles. In such cases, it is essential to establish secure communication channels that enable stakeholders to voice their opinions. This can help to overcome structural inertia. This resistance can be addressed by addressing issues and providing safe communication channels. Finally, when an organization is going through a transition, the external environment can also be a source of resistance to change management.
FAQ
How does a manager learn to manage?
By practicing good management skills at all times.
Managers must constantly monitor the performance of their subordinates.
You should immediately take action if you see that your subordinate is not performing as well as you would like.
You must be able to spot what is lacking and how you can improve it.
What is TQM?
The industrial revolution led to the birth and growth of the quality movement. Manufacturing companies realized they couldn't compete solely on price. They needed to improve quality and efficiency if they were going to remain competitive.
To address this need for improvement management created Total Quality Management (TQM) which aimed to improve all aspects of an organization's performance. It included continual improvement processes, employee involvement, customer satisfaction, and customer satisfaction.
What are the five management steps?
The five stages of any business are planning, execution, monitoring, review, and evaluation.
Planning involves setting goals for the future. Planning involves defining your goals and how to get there.
Execution takes place when you actually implement the plans. These plans must be adhered to by everyone.
Monitoring is checking on progress towards achieving your objectives. This should involve regular reviews of performance against targets and budgets.
Review events take place at each year's end. They allow for an assessment of whether all went well throughout the year. If not, changes may be made to improve the performance next time around.
After each year's review, evaluation occurs. It helps identify which aspects worked well and which didn't. It also gives feedback on how well people did.
What is the role of a manager in a company?
There are many roles that a manager can play in different industries.
Managers generally oversee the day-today operations of a business.
He/she is responsible for ensuring that the company meets all its financial obligations and produces the goods or services customers want.
He/she ensures that employees follow the rules and regulations and adhere to quality standards.
He/she is responsible for the development of new products and services, as well as overseeing marketing campaigns.
What does it mean to say "project management"
That is the management of all activities associated with a project.
This includes defining the scope, identifying the requirements and preparing the budget. We also organize the project team, schedule the work, monitor progress, evaluate results, and close the project.
What is the difference between leadership and management?
Leadership is about being a leader. Management is about controlling others.
Leaders inspire followers, while managers direct workers.
A leader motivates people to achieve success; a manager keeps workers on task.
A leader develops people; a manager manages people.
It can sometimes seem difficult to make business decisions.
Complex systems with many moving parts are the hallmark of businesses. They require people to manage multiple priorities and deal with uncertainty and complexity.
It is important to understand the effects of these factors on the system in order to make informed decisions.
To do this, you must think carefully about what each part of the system does and why. It's important to also consider how they interact with each other.
Also, you should ask yourself if there have been any assumptions in your past behavior. If so, it might be worth reexamining them.
Try asking for help from another person if you're still stuck. You may be able to see things from a different perspective than you are and gain insight that can help you find a solution.
Statistics
- This field is expected to grow about 7% by 2028, a bit faster than the national average for job growth. (wgu.edu)
- Hire the top business lawyers and save up to 60% on legal fees (upcounsel.com)
- Your choice in Step 5 may very likely be the same or similar to the alternative you placed at the top of your list at the end of Step 4. (umassd.edu)
- The BLS says that financial services jobs like banking are expected to grow 4% by 2030, about as fast as the national average. (wgu.edu)
- The average salary for financial advisors in 2021 is around $60,000 per year, with the top 10% of the profession making more than $111,000 per year. (wgu.edu)
External Links
How To
What is Lean Manufacturing?
Lean Manufacturing uses structured methods to reduce waste, increase efficiency and reduce waste. These processes were created by Toyota Motor Corporation, Japan in the 1980s. The aim was to produce better quality products at lower costs. Lean manufacturing seeks to eliminate unnecessary steps and activities in the production process. It includes five main elements: pull systems (continuous improvement), continuous improvement (just-in-time), kaizen (5S), and continuous change (continuous changes). Pull systems involve producing only what the customer wants without any extra work. Continuous improvement is constantly improving upon existing processes. Just-in-time is when components and other materials are delivered at their destination in a timely manner. Kaizen refers to continuous improvement. It is achieved through small changes that are made continuously. Five-S stands for sort. It is also the acronym for shine, standardize (standardize), and sustain. These five elements are combined to give you the best possible results.
Lean Production System
Six key concepts are the basis of lean production:
-
Flow is about moving material and information as near as customers can.
-
Value stream mapping- This allows you to break down each step of a process and create a flowchart detailing the entire process.
-
Five S's, Sort, Set in Order, Shine. Standardize. and Sustain.
-
Kanban: Use visual signals such stickers, colored tape, or any other visual cues, to keep track your inventory.
-
Theory of constraints - identify bottlenecks in the process and eliminate them using lean tools like kanban boards;
-
Just-in-time delivery - Deliver components and materials right to your point of use.
-
Continuous improvement is making incremental improvements to your process, rather than trying to overhaul it all at once.