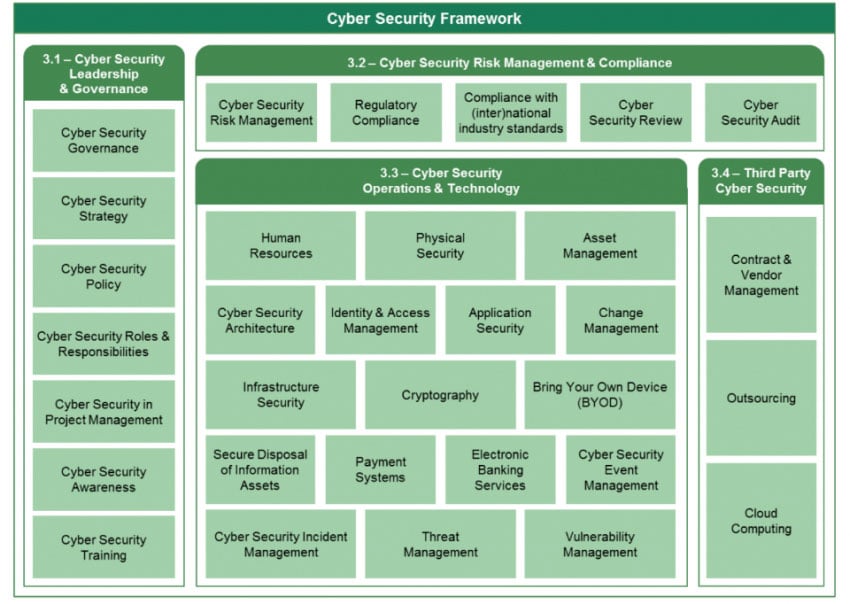
A crucial aspect of any project is construction management. A construction manager represents and oversees all aspects a project. His or her job is to complete the project on time and within budget. To fulfill the owner's expectations, he/she works together with the architect or general contractor. A construction manager must be proficient in all aspects of construction techniques and practices to be successful.
Pre-construction
The most important part of construction is the pre-construction management. It involves the management, planning, and estimation of every aspect of a construction job. It involves working together with all parties to define the design intent, requirements of the end-user, and scope of the project. The ultimate goal is to finish a project within the budget and on time.
The client and their construction partner will work together to develop detailed drawings and schedules, budgets, manpower projections, and other details. It is essential to maintain regular communication during this phase as it allows you to spot potential construction problems and help you resolve them. This ensures that the project stays on track.
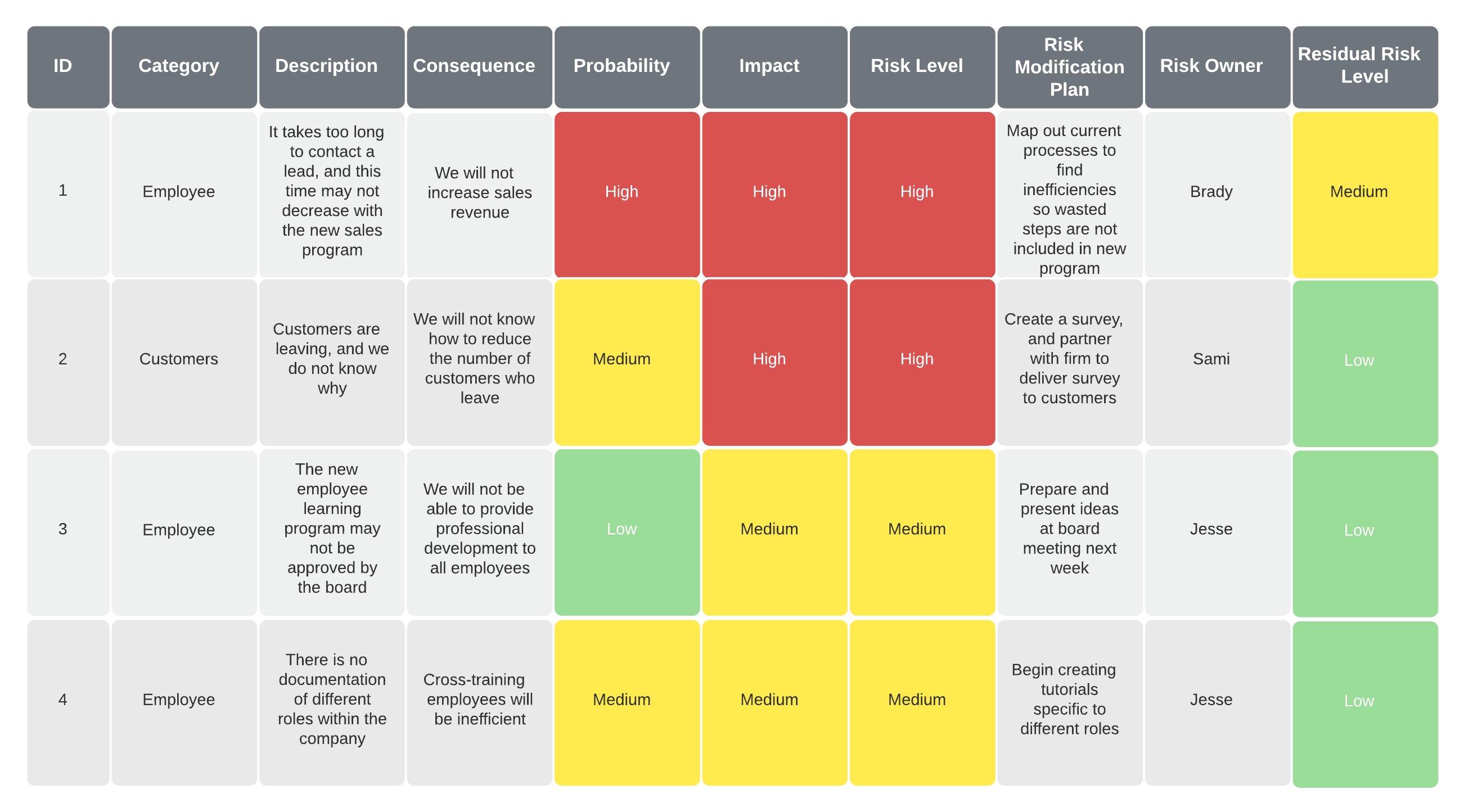
Subcontractors
Hiring subcontractors is a critical aspect of construction management. Subcontractors are a crucial part of a project's success and can play a vital role in it. Subcontractors should not be overlooked in order to avoid problems and delays. They must have a proven track record, and a reputation to deliver quality work.
Although subcontractors are independent contractors but are still employees, they are subject to the same legal protections. Understanding the legal issues surrounding subcontractors is crucial. As independent contractors, subcontractors have the same tax obligations and duties as a general contract. This could make subcontractors more susceptible to the payment of back taxes or employee benefits.
Construction project closeout
It is critical for the financial and operation health of an owner to successfully close out a construction job. As such, it's essential to plan ahead and coordinate with all the relevant parties early in the process. There are many key points to be aware of. These steps will reduce disputes and help you avoid problems. Here are some tips to help plan for a successful closeout of your project.
Construction project closeout can be a lengthy process. It includes punch lists, final inspections, and the submission of as-builts. A well-planned finalization will save time and money. It will also reduce stress for all involved, including clients and employees.
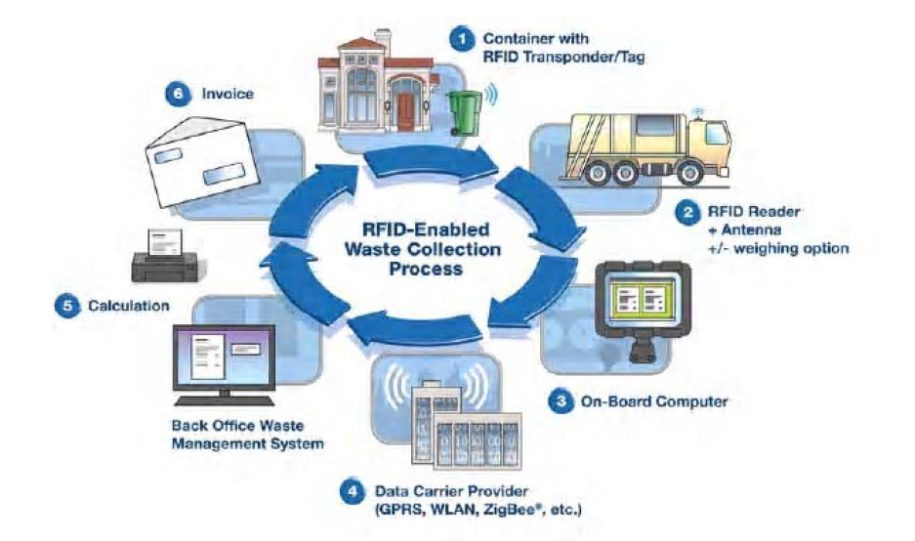
Cloud-based software
Construction management software can help you maximize your ROI. These software can automate routine tasks and integrate with other business applications. These applications allow you to manage your budget and schedules, request information from subcontractors, and make changes. Many of these applications integrate with CRM and takeoff programs. These applications can be used to manage many different types of projects.
Another benefit of cloud-based construction management software is the ability to adapt quickly to changing field needs. Cloud-based software offers users the ability to immediately access the most current features and update. No more waiting for updates.
FAQ
What are the five management methods?
Each business has five stages: planning, execution and monitoring.
Planning involves setting goals for the future. This includes setting goals for the future and defining what you want.
Execution occurs when you actually carry out the plans. It is important to ensure that everyone follows the plans.
Monitoring is the act of monitoring your progress towards achieving your targets. Regular reviews should be done of your performance against targets or budgets.
Every year, there are reviews. They allow for an assessment of whether all went well throughout the year. If not, it is possible to make improvements for next year.
After the annual review, evaluation takes place. It helps identify which aspects worked well and which didn't. It provides feedback about how people perform.
What is the difference in Six Sigma and TQM?
The key difference between the two quality management tools is that while six-sigma focuses its efforts on eliminating defects, total quality management (TQM), focuses more on improving processes and reducing cost.
Six Sigma is an approach for continuous improvement. It emphasizes the elimination and improvement of defects using statistical methods, such as control charts, P-charts and Pareto analysis.
This method has the goal to reduce variation of product output. This is done by identifying and correcting the root causes of problems.
Total quality management involves measuring and monitoring all aspects of the organization. It also includes the training of employees to improve performance.
It is frequently used as an approach to increasing productivity.
How does Six Sigma work
Six Sigma uses statistical analysis to find problems, measure them, analyze root causes, correct problems, and learn from experience.
The first step to solving the problem is to identify it.
The data is then analyzed and collected to identify trends.
Then corrective actions are taken to solve the problem.
The data are then reanalyzed to see if the problem is solved.
This cycle will continue until the problem is solved.
What is the difference between management and leadership?
Leadership is about influence. Management is about controlling others.
Leaders inspire followers, while managers direct workers.
A leader motivates people and keeps them on task.
A leader develops people; a manager manages people.
What is TQM exactly?
The industrial revolution led to the birth and growth of the quality movement. Manufacturing companies realized they couldn't compete solely on price. They had to improve efficiency and quality if they were to remain competitive.
Management realized the need to improve and created Total Quality Management, which focused on improving all aspects within an organization's performance. It included continuous improvement, employee involvement and customer satisfaction.
What can a manager do to improve his/her management skillset?
Through demonstrating good management skills at every opportunity
Managers must monitor the performance of subordinates constantly.
You must quickly take action if your subordinate fails to perform.
You should be able pinpoint what needs to improve and how to fix it.
Statistics
- This field is expected to grow about 7% by 2028, a bit faster than the national average for job growth. (wgu.edu)
- 100% of the courses are offered online, and no campus visits are required — a big time-saver for you. (online.uc.edu)
- Your choice in Step 5 may very likely be the same or similar to the alternative you placed at the top of your list at the end of Step 4. (umassd.edu)
- Our program is 100% engineered for your success. (online.uc.edu)
- As of 2020, personal bankers or tellers make an average of $32,620 per year, according to the BLS. (wgu.edu)
External Links
How To
How do I do the Kaizen Method?
Kaizen means continuous improvement. The Japanese philosophy emphasizes small, incremental improvements to achieve continuous improvement. This term was created by Toyota Motor Corporation in 1950. This is a collaborative process in which people work together to improve their processes continually.
Kaizen is one method that Lean Manufacturing uses to its greatest advantage. In this concept, employees who are responsible for the production line must identify problems that exist during the manufacturing process and try to solve them before they become big issues. This increases the quality of products and reduces the cost.
Kaizen is a way to raise awareness about what's happening around you. If something is wrong, it should be corrected immediately so that no problem occurs. If someone is aware of a problem at work, he/she should inform his/her manager immediately.
Kaizen follows a set of principles. We always start from the end product and move toward the beginning. In order to improve our factory's production, we must first fix the machines producing the final product. Next, we fix the machines which produce components. And finally, we fix the workers who work directly with those machines.
This is known as "kaizen", because it emphasizes improving each step. After we're done with the factory, it's time to go back and fix the problem.
You need to know how to measure the effectiveness of kaizen within your business. There are several ways that you can tell if your kaizen system is working. Another way to determine if kaizen is working well is to look at the quality of the products. Another method is to determine how much productivity has improved since the implementation of kaizen.
A good way to determine whether kaizen has been implemented is to ask why. Did you do it because it was legal or to save money? Did you really believe it would lead to success?
Suppose you answered yes to any of these questions, congratulations! You're ready to start kaizen.