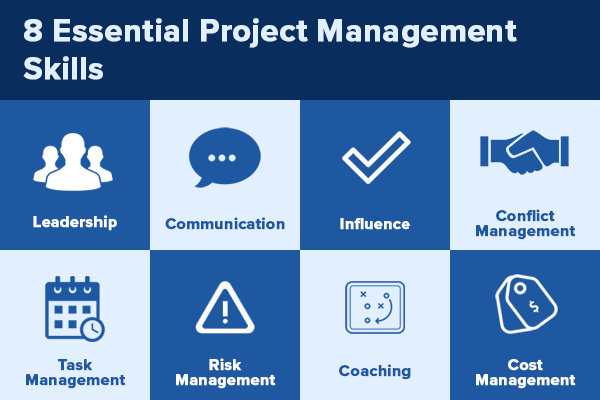
For admission to the graduate programs in msoe civil engineers, you will need an undergraduate degree. You will then need to complete 45 graduate credits. These credits can be taken from any civil engineering department or specialization, depending on what you are interested in. Additionally, you will need to score either a GRE/ACT score. Typically, admission is competitive. Apply early to ensure you get in to the program.
Graduate programs at msoe-civil engineering
Msoe offers graduate programs that allow students to select a concentration. Graduates might choose to concentrate on architecture or structural, environmental and/or hydro resources engineering, or any other broad-based topic. Students have the option of choosing from a variety of electives and evening classes in each program. Students will be able to apply engineering principles and business principles to their jobs. MSOE's Civil Engineering program prepares graduates to work in the workforce and have a positive impact on society.
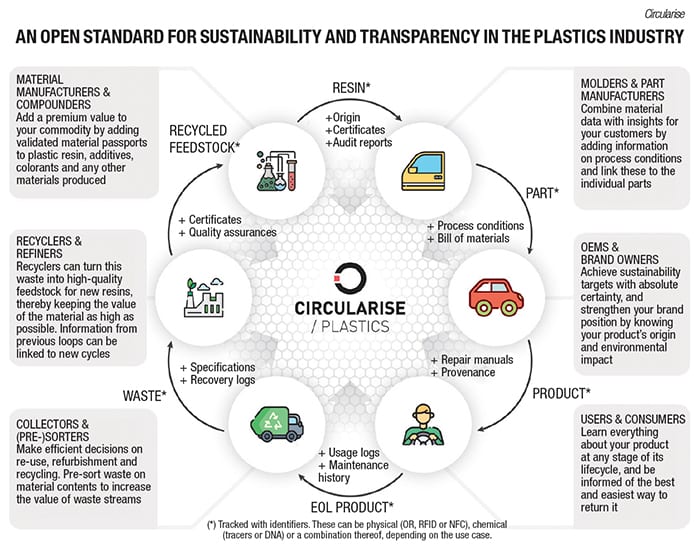
Students earn 45 credits during the MSCVE program. 36 credits must be applied towards their chosen specialization. Other graduate courses may be taken from other departments or specialty areas in civil engineering. In addition to electives, students must complete one capstone project, which is an essential part of the program. Students are eligible to apply for a MSAE examination after completing the program.
Average tuition cost in civil engineering program at the msoe
The average tuition cost for civil engineering courses at MSOE is something you should have considered if you're thinking about studying there. This university's net price is $19,790, which is higher than the national average. MSOE offers financial aid packages that are generous enough to make the cost affordable for most families. The cost of tuition at MSOE is based on the 2019-2020 IPEDS survey.
Milwaukee School of Engineering is an independent university in Milwaukee, Wisconsin. Originally known as the School of Engineering, it now offers 16 four-year credentials and has eight academic departments. It offers both graduate and undergraduate programs. The academic calendar is split into four terms of ten weeks. The summer quarter is the most popular time for students to enroll. MSOE's recent survey found that students pay an average $56,586 per year.
SAT/ACT scores required for admission to msoe Civil Engineering
The SAT/ACT scores are usually in the upper Twenty-four percent of national average. The Milwaukee School of Engineering accepts scores below this. Applicants with high ACT scores generally submit scores between twentytwo and twentythree. The average SAT/ACT composite score among successful applicants is twenty three. There is a 61percent acceptance rate at the school, with 2,192 admissions for 3,552 applications as of January 2019.
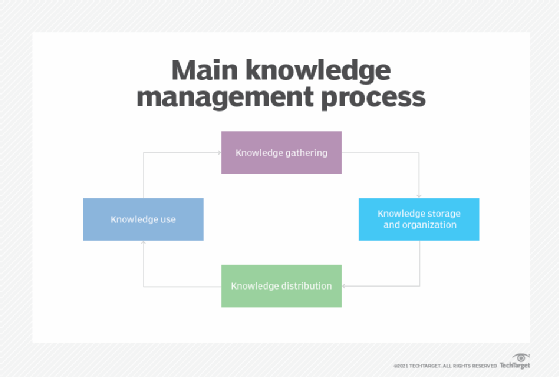
An accredited university must award a bachelor's level degree. The Graduate Record Examination must be taken within five years of the application if the applicant does not possess a bachelor’s degree. For international students, the university requires TOEFL or IELTS scores, as evidence of English Language Proficiency. Students should also submit official transcripts, and three letters from recommendation.
FAQ
What role can a manager fill in a company’s management?
Managers' roles vary from industry to industry.
A manager generally manages the day to-day operations in a company.
He/she is responsible for ensuring that the company meets all its financial obligations and produces the goods or services customers want.
He/she is responsible for ensuring that employees comply with all regulations and follow quality standards.
He/she is responsible for the development of new products and services, as well as overseeing marketing campaigns.
What are the steps in the decision-making process in management?
Managers face complex and multifaceted decision-making challenges. It involves many factors, including but not limited to analysis, strategy, planning, implementation, measurement, evaluation, feedback, etc.
When managing people, the most important thing to remember is that they are just human beings like you and make mistakes. There is always room to improve, especially if your first priority is to yourself.
We explain in this video how the Management decision-making process works. We will discuss the various types of decisions, and why they are so important. Every manager should be able to make them. The following topics will be covered:
Six Sigma is so beloved.
Six Sigma is easy and can deliver significant results. Six Sigma also gives companies a framework for measuring improvement and helps them focus on what is most important.
It seems so difficult sometimes to make sound business decisions.
Businesses are complex systems, and they have many moving parts. It is difficult for people in charge of businesses to manage multiple priorities simultaneously and also deal with uncertainty.
The key to making good decisions is to understand how these factors affect the system as a whole.
It is important to consider the functions and reasons for each part of the system. It is important to then consider how the individual pieces relate to each other.
You should also ask yourself if there are any hidden assumptions behind how you've been doing things. If not, you might want to revisit them.
Try asking for help from another person if you're still stuck. They may see things differently from you and have insights that could help you find a solution.
What are the 4 main functions of management?
Management is responsible to plan, organize, direct, and control people and resources. It includes creating policies and procedures, as well setting goals.
Management helps an organization achieve its objectives by providing direction, coordination, control, leadership, motivation, supervision, training, and evaluation.
These are the four major functions of management:
Planning - This is the process of deciding what should be done.
Organizing: Organizing refers to deciding how things should work.
Directing - This refers to getting people follow instructions.
Controlling - Controlling means ensuring that people carry out tasks according to plan.
What is the main difference between Six Sigma Six Sigma TQM and Six Sigma Six Sigma?
The major difference between the two tools for quality management is that six Sigma focuses on eliminating defect while total quality control (TQM), on improving processes and decreasing costs.
Six Sigma is a method for continuous improvement. It emphasizes the elimination of defects by using statistical methods such as control charts, p-charts, and Pareto analysis.
This method attempts to reduce variations in product output. This is accomplished by identifying the root cause of problems and fixing them.
Total quality management includes monitoring and measuring all aspects of an organization's performance. Training employees is also part of total quality management.
It is often used as a strategy to increase productivity.
Statistics
- 100% of the courses are offered online, and no campus visits are required — a big time-saver for you. (online.uc.edu)
- Hire the top business lawyers and save up to 60% on legal fees (upcounsel.com)
- As of 2020, personal bankers or tellers make an average of $32,620 per year, according to the BLS. (wgu.edu)
- Your choice in Step 5 may very likely be the same or similar to the alternative you placed at the top of your list at the end of Step 4. (umassd.edu)
- UpCounsel accepts only the top 5 percent of lawyers on its site. (upcounsel.com)
External Links
How To
How can you use the Kaizen method?
Kaizen means continuous improvement. The Japanese philosophy emphasizes small, incremental improvements to achieve continuous improvement. This term was created by Toyota Motor Corporation in 1950. It's a process where people work together to improve their processes continuously.
Kaizen, a Lean Manufacturing method, is one of its most powerful. Kaizen is a concept where employees in charge of the production line are required to spot problems during the manufacturing process before they become major issues. This increases the quality of products and reduces the cost.
Kaizen is the idea that every worker should be aware of what is going on around them. To prevent problems from happening, any problem should be addressed immediately. It is important that employees report any problems they see while on the job to their managers.
There are some basic principles that we follow when doing kaizen. We always start from the end product and move toward the beginning. If we want to improve our factory for example, we start by fixing the machines that make the final product. Then, we fix the machines that produce components and then the ones that produce raw materials. Finally, we repair the workers who are directly involved with these machines.
This is why it's called "kaizen" because it works step-by-step to improve everything. Once the factory is fixed, we return to the original site and work our way back until we get there.
You need to know how to measure the effectiveness of kaizen within your business. There are many methods to assess if kaizen works well. One of these ways is to check the number of defects found on the finished products. Another method is to determine how much productivity has improved since the implementation of kaizen.
Another way to know whether kaizen is working is to ask yourself why did you decide to implement kaizen. You were trying to save money or obey the law? Did you really believe it would lead to success?
If you answered yes to any one of these questions, congratulations! You're ready to start kaizen.