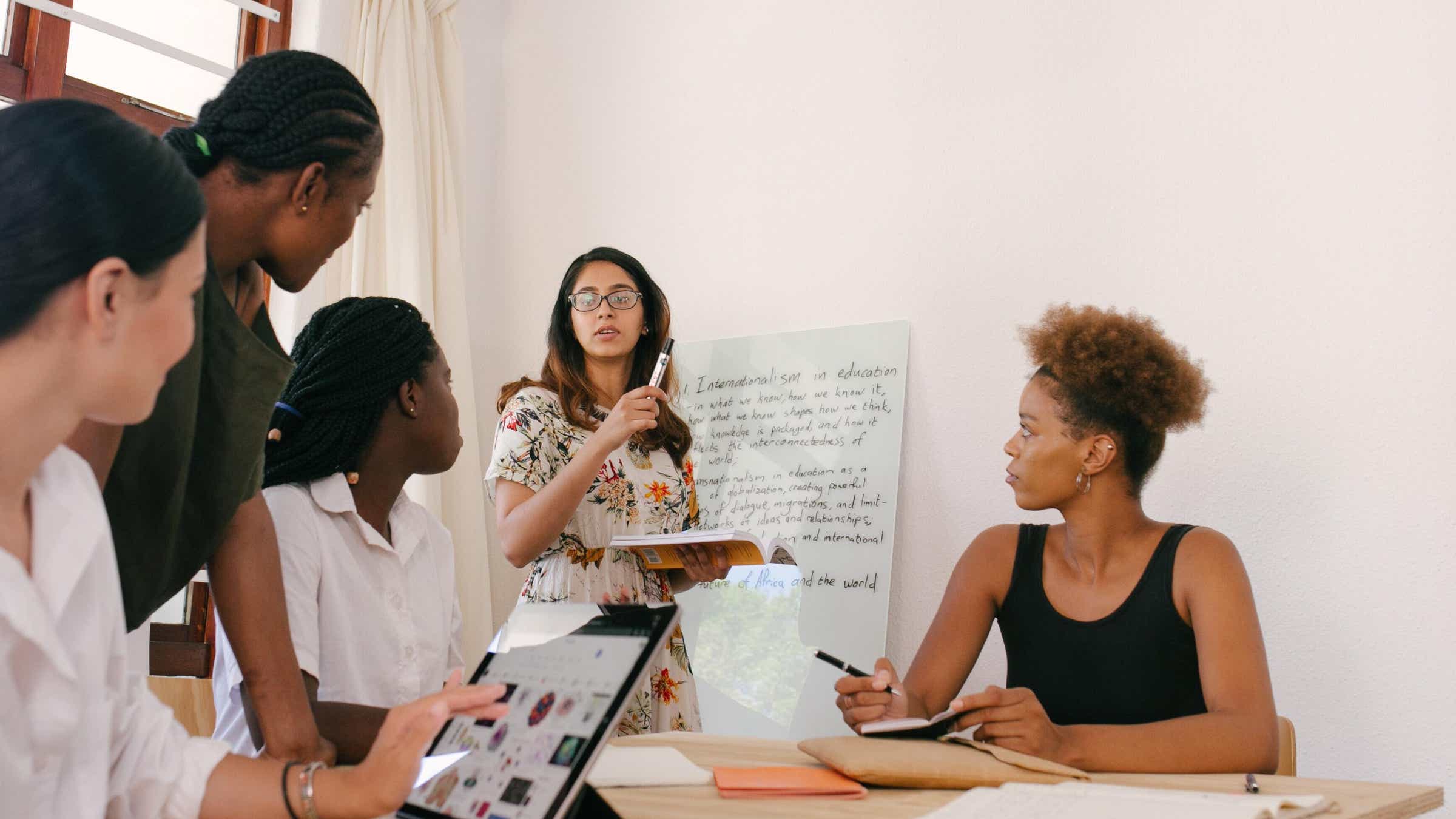
There are many aspects to risk management. Identifying threats and vulnerabilities and developing a response plan are key. Once you have identified any potential threats or vulnerabilities, you can begin the process of assessing residual risk. You will be able to see the potential impact and take the appropriate actions. These are just some of the parts. You can read more about them below. A risk management plan is crucial for any business to be successful.
Assessing residual risks
A risk assessment is an evaluation of residual risks that could be associated with a product, service, or product. A residual risk is a risk that remains after all controls have been taken. The residual risk can be categorized as inherent, mitigating, or external. It is important to decide how to treat residual risk. Additionally, it is important for the organization to perform a preliminary assessment to identify areas at risk that are beyond its risk appetite. The residual risk assessment will specify a treatment percentage based on the expected effectiveness of a treatment effort.
The nature of the vendors and an organization's risk appetite will determine the acceptable level of residual risks. Organizations of small to medium size don't usually have the risk appetite to implement a comprehensive risk management plan. They will instead use baseline or industry standards as their guide. Similar to the above, companies that evaluate their risk against industry standards will most likely be using residual risks. However, it is important to remember that these methods may lead to inaccurate reporting and a false impression of security.
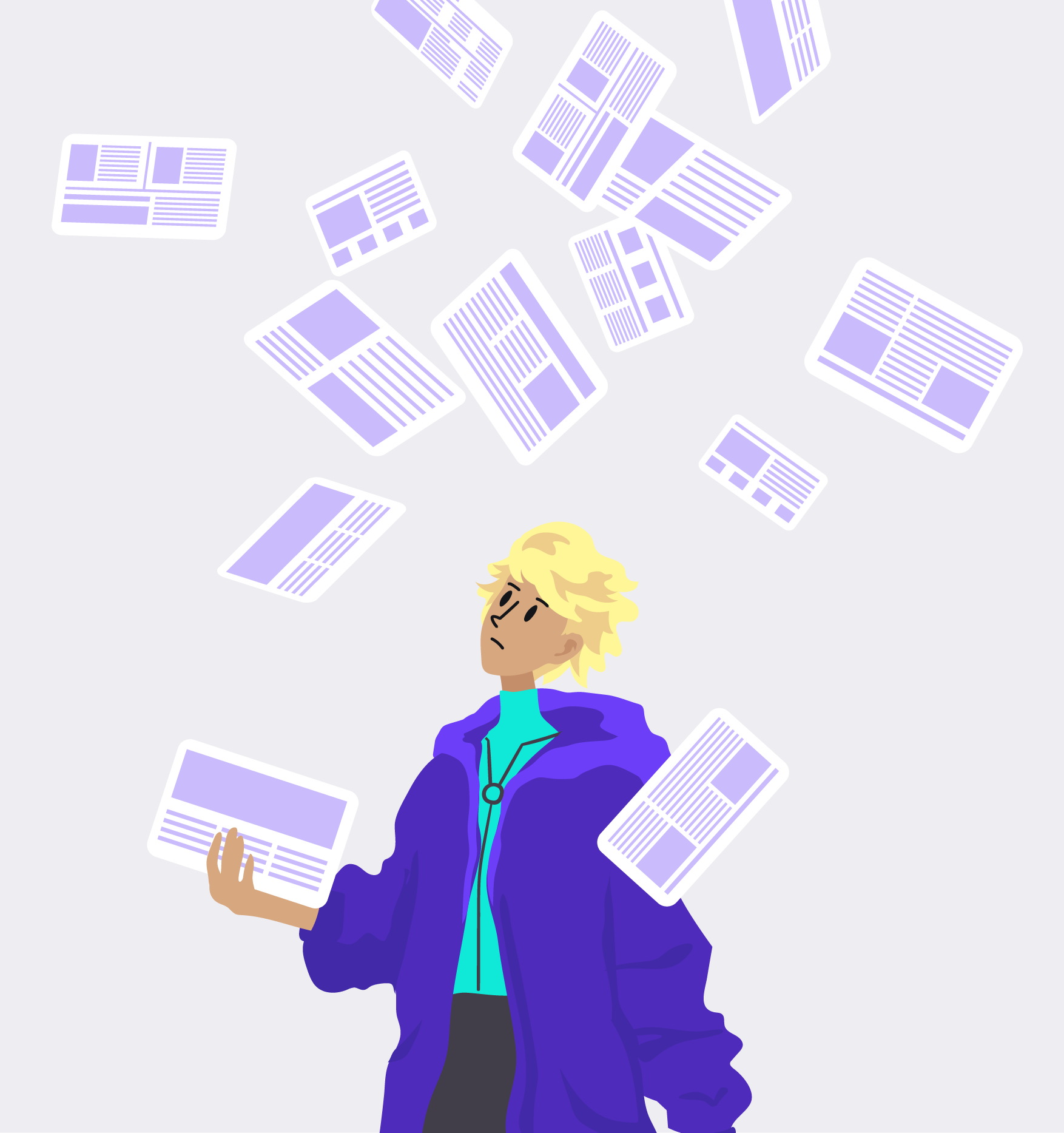
Recognizing threats
A company should identify potential threats to its organization as part of risk management. The first step in risk management is to identify potential threats to the business. Many risk factors are known by businesses. It is vital that employers consider all possible threats. You can identify threats by studying industry publications, attending industry conferences, or obtaining case studies. Some sources offer industry-specific metrics.
It is important to determine the likelihood of potential threats. A threat can be categorized into three types: medium, high, or low impact. Threats can affect your employees, business operations, assets, and reputation. These categories will help you assess the threat to your business and determine its impact. It also allows you to estimate the cost of mitigating particular risks.
Identifying vulnerabilities
Security of your business is essential if you want to identify weaknesses as part of risk management. This begins by setting up a baseline system and determining what your tolerance to risk. Then, you identify your assets, weaknesses, as well as risks. You then prioritize the changes. In addition, you must document your vulnerability findings properly. This documentation should be easily understood by non-technical staff. Here are some tips to make the vulnerability management process run as smoothly as possible:
It's important to identify vulnerabilities because it allows you to prioritize your security efforts faster and reduce risk. There are many systems that can help you assess your vulnerabilities and determine the best solutions. Some systems will help you identify the most critical vulnerabilities first. This will help reduce the possibility of a hacker attack by removing the most critical vulnerabilities first. The severity of threats can help you prioritize your security efforts.
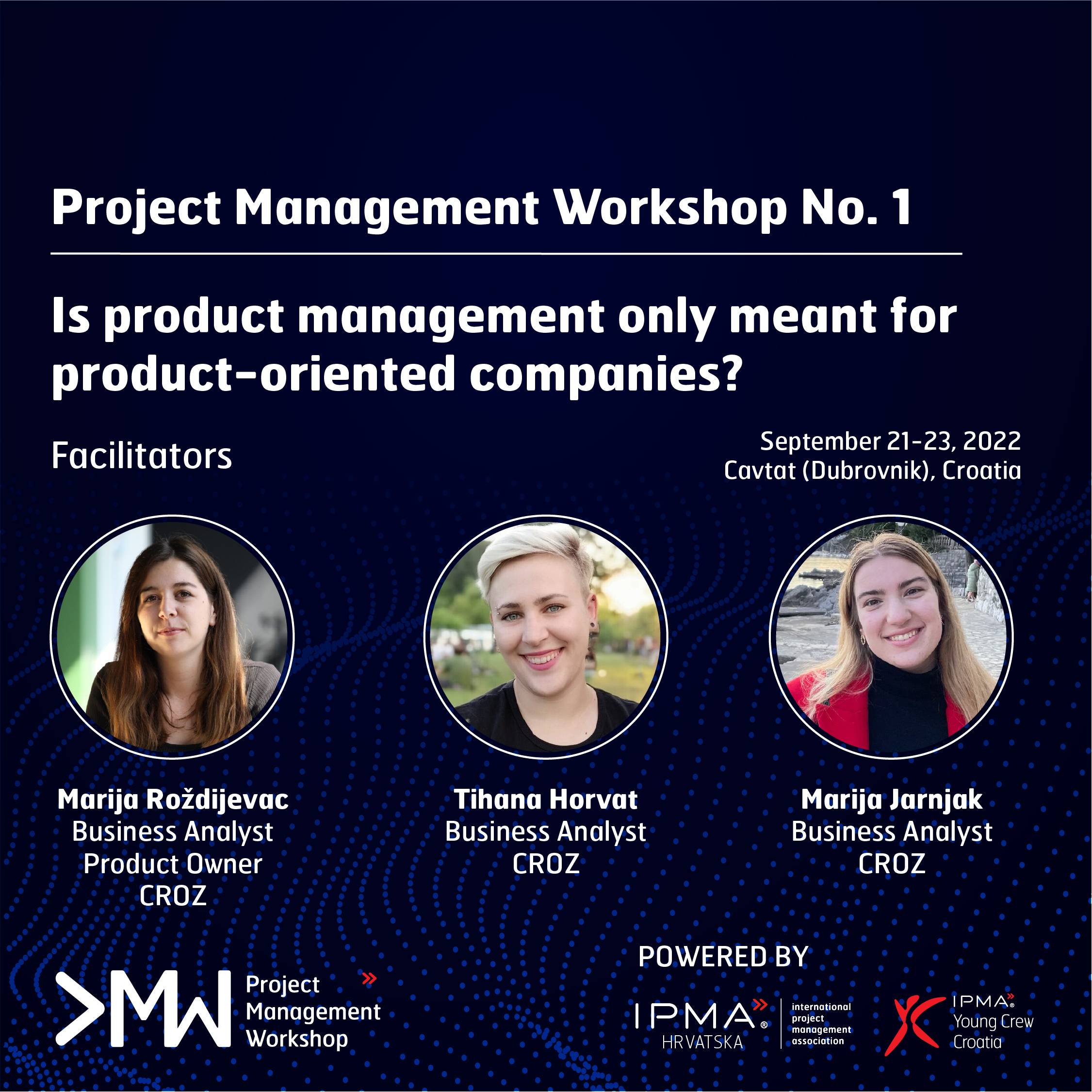
Develop a plan of action
It is crucial to develop a response plan as part the risk management process. Each risk category requires a specific response plan. These responses should be timely, cost-effective, and realistic within the context of the project. The process of creating a risk management plan involves choosing one from many options. In this article, we look at some of the common approaches to planning response plans for each risk category.
There are many strategies for dealing with each risk. The best strategy to respond to a risk is one that minimizes, or eliminates, the associated risks. These strategies can easily be identified using risk analysis tools. Next is to create specific actions that will be implemented the chosen strategies. In the event that strategies fail, fallback plans must be considered. Contingency reserves should be allocated based on the project's risk thresholds and quantitative analysis of the risk.
FAQ
How do we build a culture that is successful in our company?
A company culture that values and respects its employees is a successful one.
It is based on three principles:
-
Everyone has something valuable to contribute
-
People are treated with respect
-
Respect is shared between individuals and groups
These values are reflected in the way people behave. For example, they will treat others with courtesy and consideration.
They will listen to other people's opinions respectfully.
They can also be a source of inspiration for others.
Company culture also encourages open communication, collaboration, and cooperation.
People feel safe to voice their opinions without fear of reprisal.
They know that they will not be judged if they make mistakes, as long as the matter is dealt with honestly.
Finally, the company culture encourages honesty as well as integrity.
Everyone knows that they must always tell the truth.
Everyone recognizes that rules and regulations are important to follow.
And no one expects special treatment or favors.
What is the difference between TQM and Six Sigma?
The key difference between the two quality management tools is that while six-sigma focuses its efforts on eliminating defects, total quality management (TQM), focuses more on improving processes and reducing cost.
Six Sigma can be described as a strategy for continuous improvement. This approach emphasizes eliminating defects through statistical methods like control charts, Pareto analysis, and p-charts.
This method aims to reduce variation in product production. This is accomplished by identifying the root cause of problems and fixing them.
Total quality management refers to the monitoring and measurement of all aspects in an organization. Training employees is also part of total quality management.
It is frequently used as an approach to increasing productivity.
What are the most common errors made by managers?
Sometimes managers make it harder for their employees than is necessary.
They may not assign enough responsibilities to staff members and provide them with inadequate support.
Many managers lack the communication skills to motivate and lead their employees.
Managers sometimes set unrealistic expectations of their teams.
Managers may prefer to solve every problem for themselves than to delegate responsibility.
Why is project management so important?
Project management techniques are used in order to ensure projects run smoothly, and that deadlines are met.
This is because many businesses depend heavily upon project work to produce products and services.
Companies must manage these projects effectively and efficiently.
Companies could lose their time, reputation, and money without effective project management.
Statistics
- This field is expected to grow about 7% by 2028, a bit faster than the national average for job growth. (wgu.edu)
- Hire the top business lawyers and save up to 60% on legal fees (upcounsel.com)
- The average salary for financial advisors in 2021 is around $60,000 per year, with the top 10% of the profession making more than $111,000 per year. (wgu.edu)
- As of 2020, personal bankers or tellers make an average of $32,620 per year, according to the BLS. (wgu.edu)
- Our program is 100% engineered for your success. (online.uc.edu)
External Links
How To
How can you use the Kaizen method?
Kaizen means continuous improvement. The Japanese philosophy emphasizes small, incremental improvements to achieve continuous improvement. This term was created by Toyota Motor Corporation in 1950. It is a process where people come together to improve their processes.
Kaizen is one method that Lean Manufacturing uses to its greatest advantage. Kaizen is a concept where employees in charge of the production line are required to spot problems during the manufacturing process before they become major issues. This improves the quality of products, while reducing the cost.
Kaizen is a way to raise awareness about what's happening around you. To prevent problems from happening, any problem should be addressed immediately. If someone spots a problem while at work, they should immediately report it to their manager.
Kaizen follows a set of principles. The end product is always our starting point and we work toward the beginning. In order to improve our factory's production, we must first fix the machines producing the final product. First, we fix machines that produce components. Next, we fix machines that produce raw material. We then fix the workers that work with those machines.
This is why it's called "kaizen" because it works step-by-step to improve everything. Once we have finished fixing the factory, we return to the beginning and work until perfection.
To implement kaizen in your business, you need to find out how to measure its effectiveness. There are many methods to assess if kaizen works well. One way is to examine the amount of defects on the final products. Another way is determining how much productivity increased after implementing kaizen.
You can also find out if kaizen works by asking yourself why you decided to implement it. Was it just because it was the law or because you wanted to save money? Did you really believe it would lead to success?
Suppose you answered yes to any of these questions, congratulations! You're ready to start kaizen.