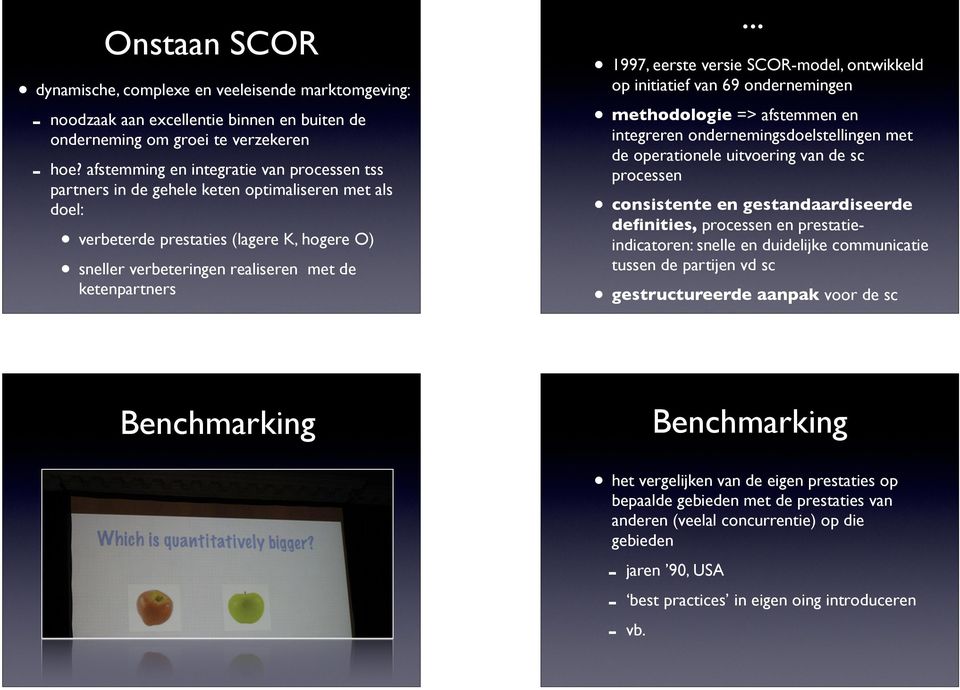
A crucial aspect of any project is construction management. The owner's interests are represented by a construction manager who oversees all aspects. His or her mandate is to ensure the project is completed on time and within budget. He or she will also work with the general contractors and the architect to meet the requirements of the owner. A construction manager should be well-versed in construction practices and methods to be successful in his or her role.
Pre-construction
Pre-construction management plays an important role in the construction process. It involves the management, planning, and estimation of every aspect of a construction job. It involves working with all stakeholders to understand the design intent, end user needs, and project scope. The ultimate goal is to finish a project within the budget and on time.
The client and the partner in construction will work closely together to produce detailed drawings, schedules. budgets. and manpower projections. Because it allows for the identification of potential problems and the resolution thereof, communication is vital during this phase. It also ensures the project follows the initial schedule.
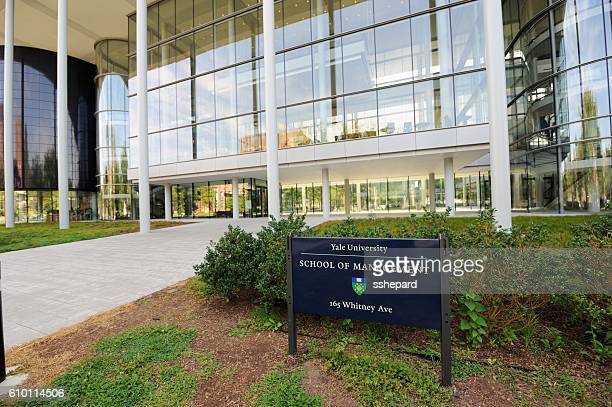
Hiring subcontractors
It is crucial to hire subcontractors in construction management. Subcontractors are a crucial part of a project's success and can play a vital role in it. Subcontractors must be chosen with care to avoid problems and delays. They must have a proven track record, and a reputation to deliver quality work.
Subcontractors, although they are independent contractors are still protected by the same legal protections that employees. As such, it is important to understand the legal aspects of hiring subcontractors. Subcontractors, being independent contractors, are subject to the same tax obligations that a general contractor. This can lead to them being liable for paying back taxes and employee benefit.
Construction project closeout
The successful closeout of a construction project is critical to the financial and operational health of the owner. It's important to plan ahead, coordinate with all involved parties early in the project. There are many key points to be aware of. Following these steps will help to minimize disputes and problems. These tips will help you plan a project closure that is successful.
Construction project closeout can be a lengthy process. It includes punch lists, final inspections, and the submission of as-builts. A well-planned and executed closeout can save you time, money, stress, and even headaches. You will save time, money, and stress for everyone involved. This includes your clients, employees, and vendors.
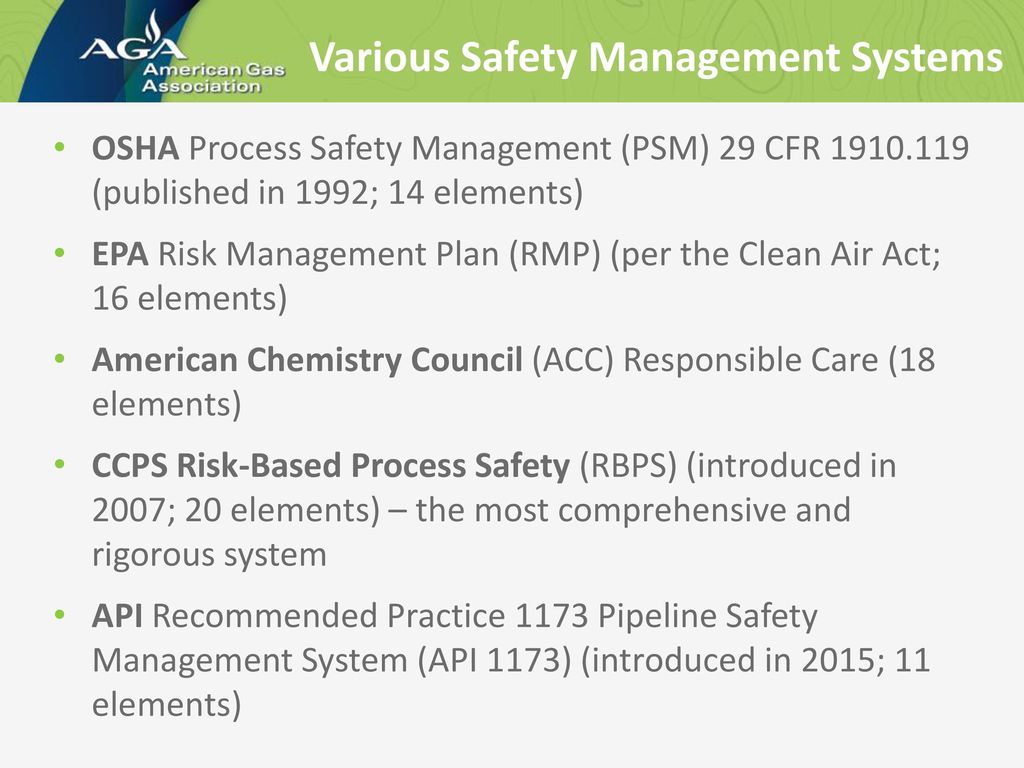
Cloud-based Software
Your ROI can be maximized with construction management software. These software solutions not only automate routine tasks, but they also integrate well with other business applications. These applications can help you monitor budgets and schedules, manage changes, and request information from subcontractors. Many of these apps can be integrated into CRM and takeoff software. You can use them to handle many types of projects.
Cloud-based construction administration software has another advantage: it can adapt quickly to changing fields needs. Cloud-based software offers users the ability to immediately access the most current features and update. This means no more delays in receiving updates.
FAQ
What is the meaning of "project management?"
This refers to managing all activities that are involved in a project's execution.
This includes defining the scope, identifying the requirements and preparing the budget. We also organize the project team, schedule the work, monitor progress, evaluate results, and close the project.
What are your main management skills
Managerial skills are crucial for every business owner, regardless of whether they run a small store in their locality or a large corporation. These include the ability and willingness to manage people, finances as well resources, time and space.
Managerial skills are required when setting goals and objectives and planning strategies, leading employees, motivating them, solving problems, creating policies, procedures, or managing change.
As you can see there is no end to the number of managerial tasks.
What is Kaizen?
Kaizen, a Japanese term that means "continuous improvement," is a philosophy that encourages employees and other workers to continuously improve their work environment.
Kaizen is based on the belief that every person should be able to do his or her job well.
How do you manage employees effectively?
Effectively managing employees means making sure they are productive and happy.
This includes setting clear expectations for their behavior and tracking their performance.
Managers need to establish clear goals for their team and for themselves.
They must communicate clearly with their staff. They need to communicate clearly with their staff.
They must also keep track of the activities of their team. These include:
-
What was achieved?
-
How much work was put in?
-
Who did it?
-
It was done!
-
Why was it done?
This information can help you monitor your performance and to evaluate your results.
Statistics
- UpCounsel accepts only the top 5 percent of lawyers on its site. (upcounsel.com)
- 100% of the courses are offered online, and no campus visits are required — a big time-saver for you. (online.uc.edu)
- The profession is expected to grow 7% by 2028, a bit faster than the national average. (wgu.edu)
- Your choice in Step 5 may very likely be the same or similar to the alternative you placed at the top of your list at the end of Step 4. (umassd.edu)
- This field is expected to grow about 7% by 2028, a bit faster than the national average for job growth. (wgu.edu)
External Links
How To
How is Lean Manufacturing done?
Lean Manufacturing processes are used to reduce waste and improve efficiency through structured methods. They were created in Japan by Toyota Motor Corporation during the 1980s. It was designed to produce high-quality products at lower prices while maintaining their quality. Lean manufacturing eliminates unnecessary steps and activities from a production process. It consists of five basic elements: pull systems, continuous improvement, just-in-time, kaizen (continuous change), and 5S. Pull systems are able to produce exactly what the customer requires without extra work. Continuous improvement involves constantly improving upon existing processes. Just-in-time is when components and other materials are delivered at their destination in a timely manner. Kaizen is continuous improvement. This can be achieved by making small, incremental changes every day. Five-S stands for sort. It is also the acronym for shine, standardize (standardize), and sustain. These five elements are used together to ensure the best possible results.
The Lean Production System
Six key concepts are the basis of lean production:
-
Flow - focus on moving material and information as close to customers as possible;
-
Value stream mapping: This is a way to break down each stage into separate tasks and create a flowchart for the entire process.
-
Five S’s - Sorted, In Order. Shine. Standardize. And Sustain.
-
Kanban - visual cues such as stickers or colored tape can be used to track inventory.
-
Theory of Constraints - Identify bottlenecks in the process, and eliminate them using lean tools such kanban boards.
-
Just-in time - Get components and materials delivered right at the point of usage;
-
Continuous improvement - make incremental improvements to the process rather than overhauling it all at once.